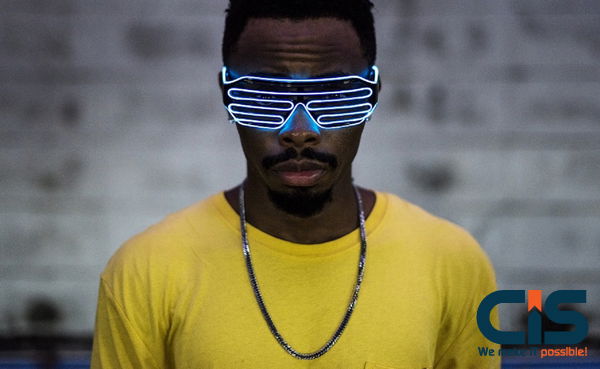
We will explore the technology enabling Industrial IoT. Additionally, we'll review its most frequent applications, benefits, and challenges so as to provide a complete view.
The Industrial Internet of Things (IIoT): What Does It Mean?
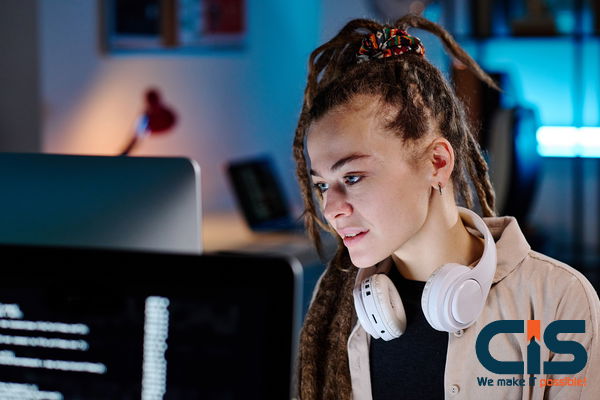
Industrial IoT (IIoT), or IoT in Industrial environments, refers to an application of IoT explicitly designed to collect data in industrial settings through intelligent connected devices such as sensors, actuators, and systems.
Cleansed, configured, and analyzed data is then transmitted directly into the cloud for accurate time delivery to managers, operators, and users for use by advanced robotics applications or robotic solutions to provide descriptive or predictive solutions or trigger entirely or semi-autonomous machine actions - making equipment more effective, decreasing human error risk while increasing worker safety while improving quality and decreasing costs simultaneously.
Industrial IoT combines devices and platforms using artificial intelligence (AI), machine learning (ML), or other software tools to form an advanced cyber-physical monitoring system that outstrips traditional manufacturing solutions regarding efficiency and capability. Statisticians project that by 2025, over 30.9 billion Internet of Things devices connected through manufacturing operations and business models will play an increasingly large part in creating business profitability, all part of Industry 4.0 or the Fourth Industrial Revolution transformation.
Also Read: This Article Will Put To Light the Most Important Issues Around IIoT
The Importance Of IIoT
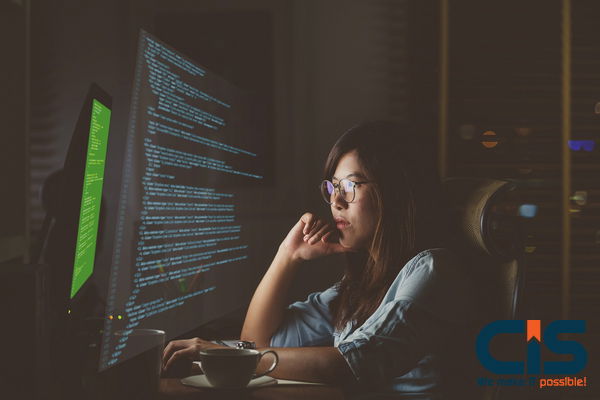
Manufacturing industries, with their combination of manual processes and reactive machine maintenance, make manufacturing an ideal place for exploiting today's massive amounts of untapped machine data. Data can be compelling; accessing it and manipulating it with business intelligence algorithms allows manufacturers to gain invaluable insights that transcend just numbers alone. Manufacturing allows manufacturers to harness this power.
Industrial IoT allows you to observe any factory from any location. At any time in real-time from any device - this way, you can precisely track each machine's status within its production cycle and see its exact condition at any given moment. Furthermore, its data and interactivity can be utilized for predictive maintenance tasks, automate processes or as required by you, and more!
Industrial IoT (also called Advanced Manufacturing) represents the future of industrial technology. Not only will passive sensors collect and analyze data for transmission or analysis, but active connections between machines to facilitate processes like self-correcting machines can occur as part of this technology.
IoT provides manufacturing processes with an opportunity to put customers first. Connectivity provides fast time-to-market, increased on-demand production capacity, and enhanced customization options. Human and machine communication will allow them to reduce repetitive manual tasks while focusing on improvements that will increase the value of manufacturing businesses.
What drives manufacturers to move towards Industrial IoT?
Industrial IoT began as an attempt to increase efficiency. Through predictive maintenance plans and historical data for future production cycle decisions, manufacturers could save time and energy by avoiding unscheduled outages while staying competitive within global markets. All this contributed to maintaining their edge within global marketplaces.
Innovation is also of great significance; manufacturers recognize its benefits of collecting large volumes of data to design new products more rapidly and affordably, meeting customer demands more effectively, with unprecedented customization capability provided through tailoring designs to individual customer specifications.
Industrial IoT creates an environment that can both be "advanced" and intelligent at the same time. Utilizing IoT data and connections can improve supply chains, including raw material supply chains, inventory control management, and demand forecasting - helping optimize all business processes by going down to the raw data level. IIoT makes data interpretation simpler by connecting any connected device directly with cloud-based software for fast interpretation, eliminating slow and error-prone processes.
Industrial IoT Solutions
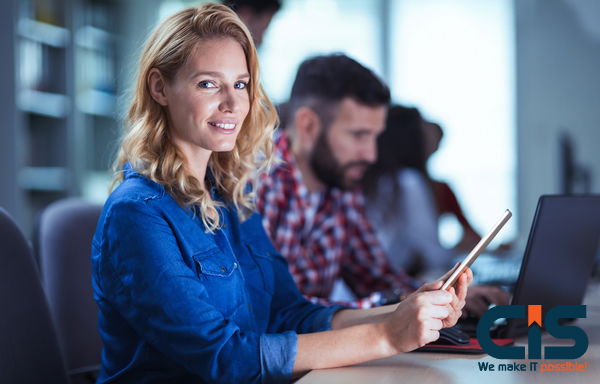
The Industrial Internet of Things relies heavily on real-time data collection. Manufacturing companies generate vast quantities of operational and transactional information every second. Unfortunately, much of it goes unused; when collected and deployed via an Industrial IoT Platform, it provides insights and solutions for numerous business requirements.
Industrial equipment is at the core of production for all markets worldwide, providing products for global marketplaces. Machine automation was traditionally performed using proprietary software designed to automate specific equipment. But with internet accessibility becoming more accessible than ever, connectivity became a much greater possibility - leading to the advent of the Industrial Internet and improved access for production machines worldwide.
IIoT are compact, user-friendly devices designed for OEM-independent connectivity between newer production equipment with embedded sensors and older analog equipment retrofitted with sensors - or vice versa - creating endless industrial applications based on data generated through normal equipment function.
Wi-Fi or cellular networks offer another means to link smart sensors with IIoT devices besides traditional T1 cables. Manufacturing companies gain complete transparency across their factory floors with integrated solutions that analyze real-time data to provide visibility into factory floors, alter SOPs, or drive continuous improvement.
An intelligent factory that captures real-time data allows manufacturers to pinpoint areas for improvement, gain actionable insights, and devise proactive strategies using prescriptive and predictive analytics.
Want More Information About Our Services? Talk to Our Consultants!
IoT vs. IndustriaI IoT
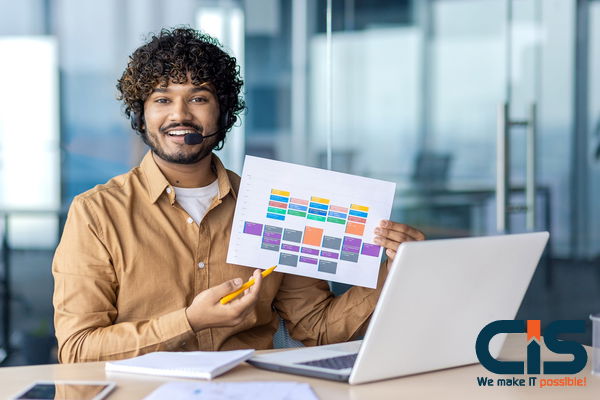
It is critical to differentiate between the Industrial Internet of Things and the Internet of Things. IoT refers to an interconnected network of devices connected via wired and wireless communications capable of gathering or transmitting data from consumer devices like cars, thermostats, and home appliances.
IIoT technologies encompass sensors, equipment communications systems, automation platforms, and analytics platforms designed to maximize industrial operations.
IIoT devices provide services that blend advanced analytics, edge devices, sensors, and communication into tailored experiences for their users. Connectivity provides advanced digital tools that use sensors, edge devices, and sensors to exchange information to control manufacturing environments more effectively and create manufacturing ecosystems.
What Are The Advantages Of IIoT?
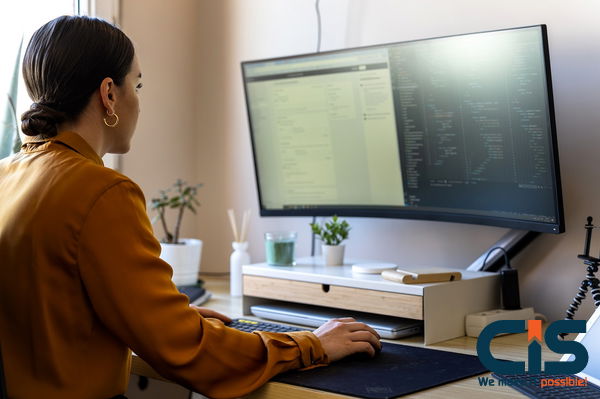
Industrial IoT solutions enable manufacturers to utilize operational data more effectively by collecting and standardizing it in real-time, which opens up an infinite number of use cases ranging from monitoring equipment downtimes, predicting trends using historical information, or monitoring equipment upkeep issues - these are among the many advantages provided by IoT solutions.
Improved Manufacturing Processes And Productivity
Human intervention can be slow and error-prone; manufacturers can instead make data-driven decisions by analyzing real-time information.
Advanced analytics can identify patterns not previously discovered and offer solutions for improving global production processes. They also highlight differences in operator performance, shift variations, and other areas to help maximize labor and capacity usage and unlock hidden capacities that boost Productivity.
Better Inventory Management
Inventory has never been more vital to supply chains than now, with prices continuing to soar and costs increasing rapidly. Industrial control systems that utilize IoT collect information beyond production floors; devices centered around conveyance or API connections collect data from all over a company using various conveyance means.
Advanced analytics this platform provides include considering finished goods' availability and impact. Once collected, data may be sent directly to finance software or ERP systems for inventory control.
Precision Quality
Traditional quality programs focus on auditing and inspecting, but in industries like CNC machining, where components for medical, automotive, and aerospace require precise tolerances, even minor variations can result in high scrap rates at the shop or safety failure when reaching end users.
IIoT devices enable operators to quickly analyze production unit parameters and make necessary adjustments before production units stray from predefined limits - saving time, materials, labor costs, and wear on equipment. This analysis helps reduce time wastage.
Spindle and engine frequency data can now be recorded, making machine-learning algorithms that detect failures or quality loss more accessible. Furthermore, many quality adjustments can now be programmed into IIoT platforms via edge devices, edge computers, or native IIoT capabilities.
Cost Savings
IIoT technology can save manufacturing companies money. Detecting anomalies quickly and resolving them efficiently saves labor, material, and downtime expenses; furthermore, it identifies patterns or trends humans might miss by using advanced analytics on collected data - this helps achieve process optimization with decreased operational costs. Connected devices provide insight that enables companies to develop strategies for predictive maintenance to reduce downtime, lower spare part costs, and extend equipment lifespan.
Asset Tracking And Protection
Capital equipment costs can be an ongoing expense for manufacturing firms, employing IIoT, real-time tracking, predictive maintenance prescriptions, and other tools to maintain asset health in one facility or across an enterprise.
An analytics platform that analyses machine data, can quickly spot issues related to tool life expectancy, machine health, and other variables that impede machine functioning and prescribe solutions that keep machines functioning at optimal performance.
Improved Product Design
Traditional product design was disconnected from manufacturing and cumbersomely iterative. It lacked real-time production data that could inform its design process and increase R&D costs and development timeframe.
IIoT technology enables designers and developers to link design and development processes with real-time operating data, which can then be used to create digital twins of products' lifespan and identify problem areas - providing designers with insights to correct design flaws while creating products with better performance characteristics.
These insights enable companies to devise proactive and business-minded strategies to reduce development costs, boost revenue streams, or introduce innovative products or services.
Which Industries Use IIoT?
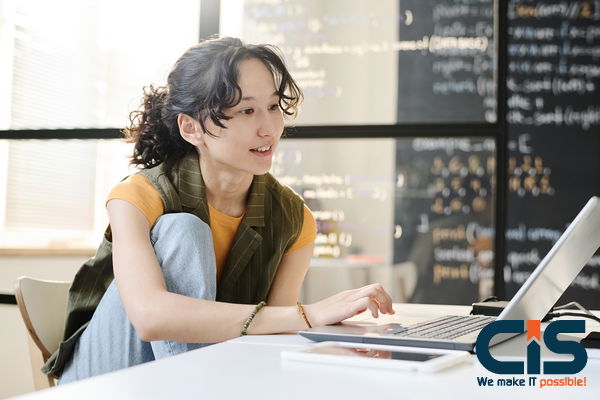
Many industries rely on IoT devices and technology, including but not limited to:
Electric Utilities
Electric utilities boast vast resources beyond production. Improve energy management and production by employing deep analytics to monitor consumption patterns and predict trends. Digital tools enabling producers to visualize network health have proven invaluable for making an impactful difference in production practices.
Oil and Gas Industry
Industrial environments vary considerably by industry. Gas production involves large footprints and long distances. Automating tasks that were once performed manually is paramount in industries where early detection can prevent environmental disasters while improving worker safety.
Automotive Industry
Automotive industries have rapidly adopted technology from the fourth industrial revolution. These high-ticket industries combine IIoT with emerging technologies like robotics to build intelligent factories.
Automotive industries make considerable investments in software. IIoT enabled these industries to develop an ecosystem for production and manufacturing monitoring linked directly with sales, marketing, and supply chain - giving a comprehensive view into manufacturing conditions while simultaneously tapping into an ever-increasing level of onboard connectivity data.
CNC Machining
CNC machine manufacturers are discrete manufacturers. Due to the nature of producing discrete items, these manufacturers typically experience challenges related to setup time and settings adjustments, process optimization, and labor training. Big data analytics and IIoT apps may have an immediate positive effect on profitability.
A CNC machine manufacturer can maximize capacity and decrease costs by analyzing data derived from sensors, retrofitted equipment, frequency data, and other inputs. This can be accomplished via improved processes, shop floor redesign, predictive maintenance, and optimized tool life optimization. Discover how manufacturers employ IoT to unlock critical use cases through our eBook.
Challenges and Risks
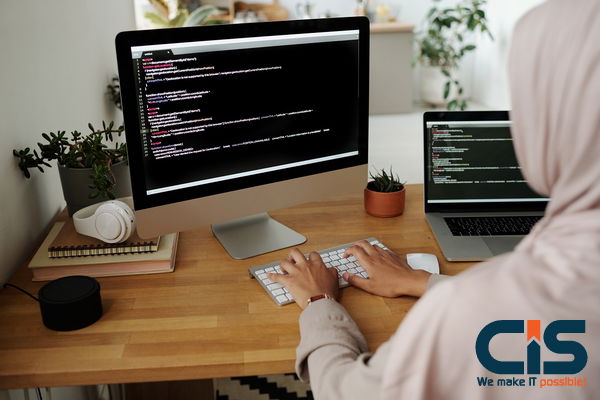
Cost, expertise, and security concerns associated with industrial IoT present themselves. Below, we explore these challenges and risks further.
Investment Cost
Costs associated with adopting and implementing any new technology should always be carefully considered when adopting any new solution. Like other industries, manufacturing companies tend to view any emerging tech through traditional IT lenses; infrastructure costs for closed network on-premise systems can be high and may prove hard or even impossible to replace or obsolete them as quickly.
A lack of understanding regarding ROI can also be present. If the IIoT benefits meet expectations, their costs should outweigh them; as device proliferation and software advancement progress, investment costs will undoubtedly decrease for ad hoc systems, affordable devices, cloud services, and software available that should help maximize return.
Training
Many operators and IT personnel resist IIoT after undertaking numerous "next big thing" projects and training classes.
Staff knowledge depends heavily upon how IT infrastructure has been designed; to maximize their Productivity, staff must learn about advanced analytics and digital tools to assist their work more efficiently.
Security
Security concerns for prospective IIoT users remain essential, particularly given that over half of critical infrastructure operations use outdated software solutions. With that being said, mobile and web interface security and weak encryption measures may pose issues when used for IIoT purposes - this is understandable, given how prevalent such concerns may be in critical infrastructure operations today.
IIoT security can be seen positively and negatively; cloud-based services have significantly enhanced IIoT protection over recent years. Currently, most breaches result from weak passwords and actions taken by companies rather than cloud providers - meaning security remains essential. Still, it ultimately lies with these organizations to control data access and ensure access controls work correctly.
What Does The Future Of IIoT Look Like?
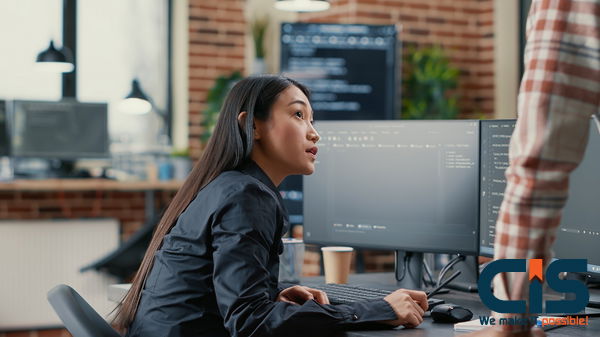
Many companies are only just getting underway with IIoT implementation despite it being one of the most exciting technologies today.
Future IIoT deployment will feature more connected devices, increased security measures, and lower adoption costs; growth should average 16.7% from 2022-2027 to reach $263.4 billion.
Adoption costs should decrease as more software and device vendors enter the market, and companies achieve double-digit productivity gains as perceptions of cost and benefit rapidly change in pursuit of a competitive edge.
Also Read: IIoT Architecture Explained With Benefits and Examples
How To Start Implementing Industrial IoT Solutions
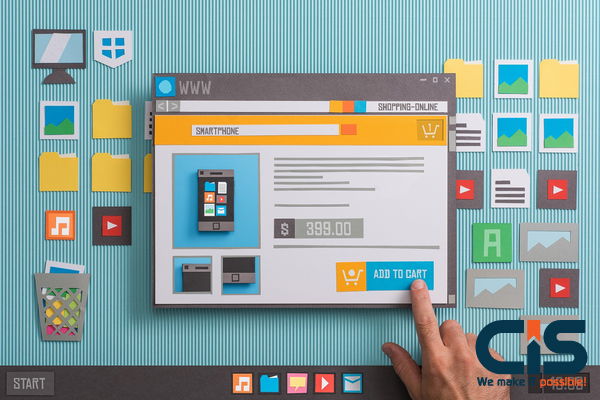
Machine monitoring is the perfect example of Industrial IoT at work. What was once a highly manual process now gives users real-time access to machine-generated data while breaking through any functional silos within organizations to enable quicker, more targeted decisions at every level of an enterprise.
Data collected automatically by machines is being utilized for real-time notifications, visualizations, and historical analytics to assist factory workers in making better decisions (Source). (Source).
Understanding and meeting the unique challenges associated with IoT in manufacturing are central to its success.
- Retrofitting older machines with internet-based technologies is often the only solution to make legacy equipment compatible with today's tech landscape. Since many manufacturers don't have enough budget to purchase brand new units, Industrial IoT requires retrofitting old units. Machine monitoring capabilities are enabled via adaptive cameras and sensors, which enable comprehensive unit tracking as well as data gathering on an unprecedented level.
- Secure connectivity and stable connectivity: To access data, wireless technology is required as an integral component of an IT infrastructure. Unfortunately, not only WIFI wireless routers do; the connectivity must also be protected with data encryption and authentication as bandwidth usage grows exponentially - once again regressing connection stability when adding bandwidth usage again. Setting up this IT infrastructure correctly takes time and money. Still, the benefits from real-time cloud connectivity will quickly outweigh these expenses!
- As the Industrial IoT industry is still young, best practices remain scarce in specific areas such as security. To minimize disruption and ensure system integrity, plans for potential compromise of systems must be implemented as soon as possible and for handling an incident after it happens.
Top 8 IoT Applications For Logistics
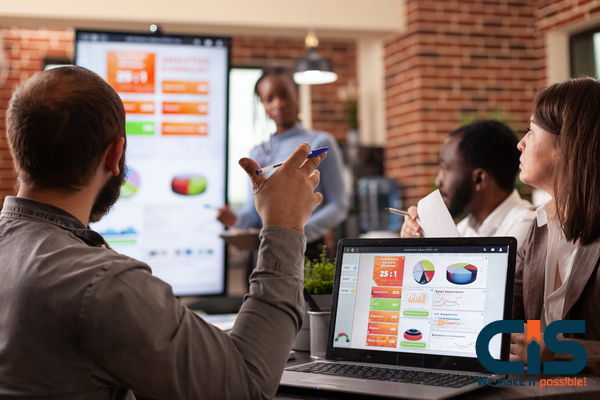
IoT adoption by logistics and transportation industries has increased exponentially over time, helping logistics providers provide excellent services while simultaneously optimizing costs as operating standards increase. Applications utilizing IoT technologies for this sector represent robust digital transformation efforts, covering warehousing, fleet management, and cargo tracking use cases across their supply chains. These top seven IoT applications demonstrate how IoT can be effectively employed for supply chain management.
Inventory Tracking and Analytics
There are multiple approaches for tracking inventory in an open and accountable fashion. Smart labels and RFID tags offer more automation and analytics capability than traditional barcodes, using microchips embedded with product information to keep inventory movements in real-time and automate item-in/item-out scanning to reduce error-prone manual processes and increase accuracy.
Optimized Warehouse
Remote warehouse condition monitoring offers many advantages to warehouse managers. Companies can establish simple rules to help regulate temperature and humidity levels within a facility; IoT sensors provide perimeter security; fleet management solutions monitor equipment workload; inventory tracking allows companies to pinpoint individual physical assets stored quickly. Fleet monitoring solutions enable fleet managers to monitor workload levels; fleet tracking solutions allow fleets of equipment to monitor fleet maintenance operations; inventory tracking solutions allow complete visibility down to individual items stored.
Real-Time Fleet Management
Fleet management is one of the most prevalent IoT logistics solutions, using GPS or satellite trackers as vehicle telematics devices to improve driver compliance, delivery accuracy, and cargo safety - ultimately improving business. Fuel consumption and driver behavior monitoring may also be included within fleet management solutions to understand each driver better individually, creating customized training programs tailored to their professional development and job satisfaction.
Predictive Maintenance
Managers of large fleets such as vehicles, warehouses, or marine equipment often struggle with cutting maintenance costs. Companies could lose millions due to unscheduled downtime and malfunctions; IoT provides another viable solution called predictive maintenance that engineers can utilize. Engineers can detect early signs of malfunction by retrofitting machinery with sensors for monitoring heat, vibrations sound levels and other parameters remotely - this also eliminates physical inspection requirements as data collected remotely allows engineers to assess vehicle health remotely.
Cargo Integrity Monitoring
Logistics firms need IoT technology even more as cargo integrity directly influences not only operational efficiency but customer satisfaction as well. Smart labels can assist logistics firms by monitoring individual items or containers during transportation - especially perishable items that could perish otherwise; as well as being used to track theft or misuse and mishandling incidents; they're even used as end-to-end tracking solutions with applications and tags to monitor cargo!
End To End Delivery Tracking
One of the key challenges of logistics is creating an intuitive dashboard to display data collected by IoT solutions, such as connectivity sensors. Modern IoT platforms offer configurable dashboards with flexible functionality so managers can stay abreast of operational information as soon as it arrives and respond to customers by quickly showing when their goods will arrive.
Last-Mile Delivery Innovations
Last-mile delivery services will see some of the most innovative IoT innovations implemented. While customers may pay extra for same-day service, companies typically find this a premium offering. Automating and speeding up supply chain workflows are necessary in order to reliably provide this service; mobile apps, smart buttons, drones and predictive replenishment will all play key roles in speeding last mile deliveries.
Integration Of IoT With Business Systems
Many companies experience difficulties when trying to integrate IoT devices and applications such as ERP or accounting with existing business applications, like ERP or accounting programs. Even IoT providers might not be willing or capable of providing additional engineering efforts needed for successful integration. Businesses looking to streamline this process need to implement modern cloud-based architectural models and centralized data integration services; otherwise, IoT ecosystem is likely to grow over time. At times it can be useful if all your IoT applications were integrated via one platform, to simplify data sync and provide tools necessary for scaling solutions. Furthermore, managing multiple apps under a centralized interface and connecting with various other systems would prove immensely advantageous.
Logistics companies should develop comprehensive strategies for their Internet of Things initiatives. Modern technology offers transformative capabilities that will revolutionize supply chain management; but its usage should not be random; rather, its seamless implementation into your supply chain while taking advantage of new IoT capabilities will allow your innovation processes to move more swiftly while remaining agile in response.
Want More Information About Our Services? Talk to Our Consultants!
Conclusion:
Cyber Infrastruture Inc. provides the ultimate platform for collecting, managing, analyzing and taking action on data generated from manufacturing equipment. Connectivity via plug and play machines combined with user-friendly apps as well as powerful integrations help turn machine data into actionable insights that empower frontline workers, other factory systems and machines themselves to operate more effectively.
Used by hundreds of manufacturers around the globe to monitor production, identify bottlenecks and predict machine failures, as well as automate workflows for manufacturing equipment.