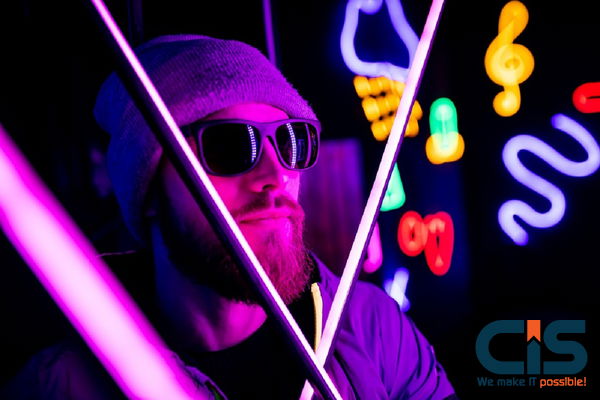
- You can manage work across systems and teams with Procurement Operation Management. This allows you to Automate and capture non-structured, repeatable work to refocus teams on higher-value work.
- Reduce onboarding and qualification cycles with guided collaboration, configurable step-by-step playbooks, and customizable step-by-step guides.
- Automated order creation and centralized catalogs can improve compliance and contract usage.
- This solution will also help you increase engagement through collaboration, self-service, and omnichannel access. Self-service interactions can deflect requests not focused on the correct issues from suppliers and employees.
- Automate the first request by streamlining intake.
- Meeting employees and suppliers at their workplaces will improve governance and spending management.
- Intelligence can be used to improve processes continuously. You can: Transparency improves supplier compliance and spending governance.
- Allow suppliers to help you better by letting them define and update their information.
- Improve your results by improving the people, processes, and behaviors.
Many enterprise transformation projects include procurement. Procurement leaders evaluate their priorities to find transformative ways of improving procurement processes while taking advantage of existing investments. Organizations can use Procurement Operations Management (POM) solutions for multiple use cases.
Enhance Procurement Processes And Ensure Compliance
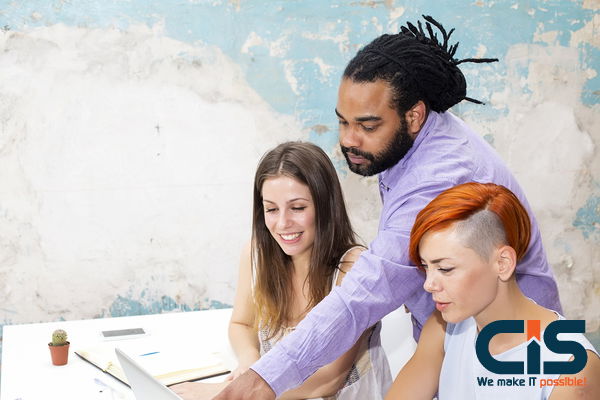
Virtual agents, knowledge bases, and intuitive workflows enable employees to self-service their requests independently. Omni-channel experiences that meet employees at their workplaces can increase employee engagement and spending under management. Playbooks with step-by-step instructions make processes simpler to track and more efficient; controls in digital workflows may increase contract utilization and compliance.
Improve Accuracy And Speed Up Supplier Qualification
Expand the procurement process by including supplier qualifications and onboarding. Workflows can be orchestrated across teams from finance to legal. You can improve suppliers' quality by giving suppliers control of their data management and providing suppliers more responsibility to take on cases and tasks to accelerate resolution timeframes faster.
Digital Experiences Transform Supplier Management
Real-time collaboration with suppliers on case management allows you to resolve quality resolutions and shortages more effectively and centralize all information about supplier performance, environmental, social, and governance (ESG), and demographics data - helping better manage supplier data. Utilize third-party intelligence on suppliers to increase depth and breadth.
What Is Operational Excellence?
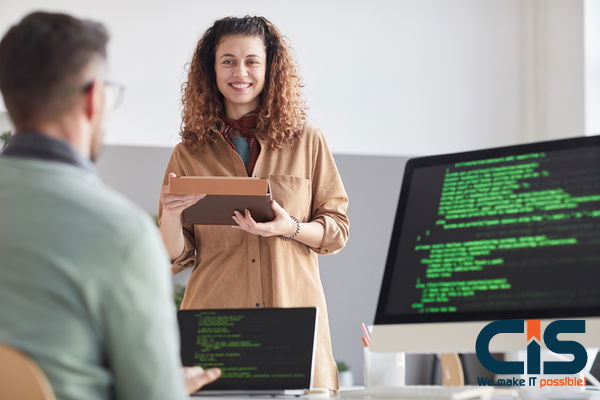
Operational Excellence is a strategic goal that drives business performance by lowering costs and risks while providing superior service quality through transparent, efficient practices.
Operational Excellence, also referred to as Operating Excellence or Operations excellence, refers to improving business performance through efficient, transparent, and value-adding practices that reduce operating costs and risks while providing improved service quality to an enterprise. OpEx may be used interchangeably as shorthand for operational excellence and managing quality integrations servicenow.
Why Is Operational Excellence So Important?
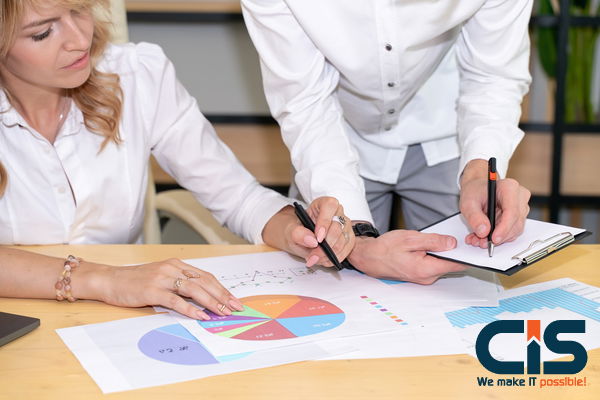
A strong foundation is essential to achieving the desired state. Organizations need it to align and work together. Business leaders can address the most common pressures across their operations by implementing a unified organizational strategy to achieve operational excellence.
- Reduce costs and run their enterprise services operations efficiently.
- Communication of ESG commitments to stakeholders
- Demonstrating resilience to investors
- Scaling up their business to be efficient and effective
What Are The Advantages Of Operational Excellence?
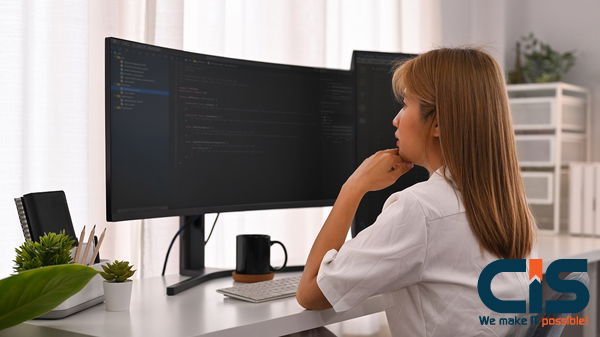
Different parts of your company work better when they are working together. This could mean combining business management, social media, governance, and security into one operational platform, depending on how your business operates. This allows you to build transparent, effective, and trustworthy processes. Your organization can then better serve your customers, staff, or even the planet. Some of the other benefits are:
- Leaders can remain strategic.
- The organization can create a competitive advantage.
- Maintaining the values of sustainability among your colleagues and customers can have a positive impact on the environment.
Global Business Services (GBS)
Global Business Services is an organizational model that aims to provide end-to-end business services in a single department. ).
GBS organizations can be put in place for several reasons, including to improve service quality, governance, and scale delivery. GBS organizations are asked to deliver advanced enterprise capabilities like analytics, continuous improvement, and transformation.
GBS integrates these previously separate and siloed operational support functions within a single corporate service organization. Organizations that achieve efficiencies with GBS strive to:
- Connecting end-to-end process while reducing costs
- Employee service experience unified.
- Shared visibility across all service cases
- Easy and rapid continuous improvement
Real-Time Risk And Resilience
What does it mean for an organization to be "risk resilient"? Risk-resilient organizations possess the resources and processes to anticipate, address, and seize future challenges while taking advantage of opportunities. Businesses that manage resilience and risk in real time are even more powerful.
Governance, Risk, and Compliance programs assist enterprises with mitigating risks and complying with compliance mandates. This area has become even more critical as businesses adopt cloud platforms and digital transformation. While these advances enable customers and employees to access digital services easily, they also increase risks.
Outdated GRC tools and processes expose organizations to unnecessary risks, placing them at a distinct disadvantage. Businesses could offset this situation by incorporating modern risk management and regulatory compliance practices into digital workflows to gain new insights and make better decisions.
Strategic Results
Organizations can achieve their strategic goals more efficiently by shifting their traditional Project Portfolio Management practices into Strategic Portfolio Management (SPM). SPM allows organizations to fund and prioritize what's most essential, layout plans for investment decisions, communicate goals to team members, and track progress; teams can plan work that fits best into their daily lives while meeting business demands with ease.
Organizations must take three steps to create a SPM environment.
- Maximize your results with a roadmap strategy.
- Aligning investments with strategy
- Any method will work to deliver value quickly.
Environmental, Social, Governance
Environmental Social Governance (ESG). It is designed to promote business growth while creating a more sustainable, ethical, and equitable world for future generations.
Organizations that operate responsibly and look for opportunities to address social challenges can offer solutions to issues like poverty, inequality, and starvation. Private sector innovation is on the rise; when companies demonstrate good corporate citizenship by adopting positive environmental and social practices that benefit both their consumers and the planet, the rewards can be enormous.
Most organizations actively participate in ESG activities, but only some possess an enterprise-wide planning and operational model or technology infrastructure that will enable them to meet their ESG goals as the demands for this responsibility grow.
Integrating ESG workflows onto one platform to operationalize its pillars is an industry best practice in ESG. When combined with operational controls for strategizing, managing, governing, and reporting ecosystem-wide strategies, this approach breaks down silos while aligning investments with goals; while also aligning ESG with corporate priorities and processes for optimal results.
Automation improves employee and customer experiences; customers will appreciate your ability to provide high-quality service in unpredictable situations.
Contact center agents may sometimes not be the most suitable people to address customer service issues. Customer self-service offers another solution, and support agents often require collaboration across other teams to resolve more complex problems quickly and efficiently. This automation example aids operational excellence.
Four Steps to Building Operational Excellence In Procurement
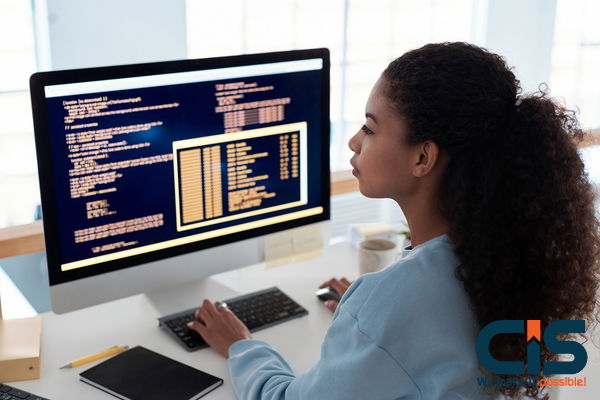
Procurement's incredible versatility lies in its ability to adapt quickly to whatever business needs arise at any given moment - supply shortage? Procurement will find it. Costs rising? The procurement department can control it. And are sustainability and diversity high on executives' agendas? Sustainability and diversity initiatives in procurement have seen increased implementation over the years.
Now is the time for procurement professionals to improve their game and gain a reputation as high performers. "During the pandemic, attention was drawn sharply to supply chains; this increased the stakes for supply chain practitioners as challenges and opportunities presented themselves," explained Mr. Sahu.
Today's business climate requires a greater focus on cybersecurity, socially responsible spending, and third-party risk management. These challenges are amplified by chronic shortages of labor and supplies, along with rising inflation rates.
Chris is an optimistic person who always sees things from an optimistic viewpoint. He firmly believes that procurement has the opportunity to optimize its strategies and processes to reach operational excellence, so here are his four steps for us all to get there:
Step 1. Get A Data-Driven, Consolidated Overview Of The Available Opportunities
Start with the sourcing process and then manually review all sourcing and contracting systems. This will help you capture and centralize any forward-looking opportunities. Engage with business partners to understand their current and forecasted demand, and consider employing tools such as a 'start-stop-continue' review process to identify areas for improvement and ensure a consistent focus on the right things.
Step 2. Build A Sustainable Digital Process
The investment in step one justifies the creation of a sustainable process. Assure that technology and processes 'feed' the pipeline with contracting, review, and sourcing opportunities. Once this step is completed, procurement should have a much better understanding of the work that needs to be done procurement service management servicenow.
Step 3 - Measure and Analyze
Based on the relative complexity of each project, it is possible to develop standard processes and timelines for all projects. The more data that procurement gathers about its workflows, turnaround times, and other factors, the better equipped it will be to estimate accurately how long future projects will take and to find ways to improve process efficiency.
Step 4: Optimize Your Procurement Process
After measuring and analyzing their efficiency, procurement can identify areas for improvement, such as reviewing the sourcing process, challenging excessive approvals, or addressing capabilities gaps through automation and training. At this stage, the goal is to optimize procurement and reduce inefficiency. This will ultimately transform procurement into a highly performing-function.
Procurement evaluates the return on investment of the company's spend. However, they should also consider the ROI for their different activities. It will be easier for procurement to prioritize their time and efforts if they understand the benefits of each capability and what the company expects procurement to achieve. Procurement functions that are high-performing focus on activities with high returns.
Also Read: Want to Be a ServiceNow Developer? Key Steps and Skills Needed
How Can You Achieve Operational Excellence Using?
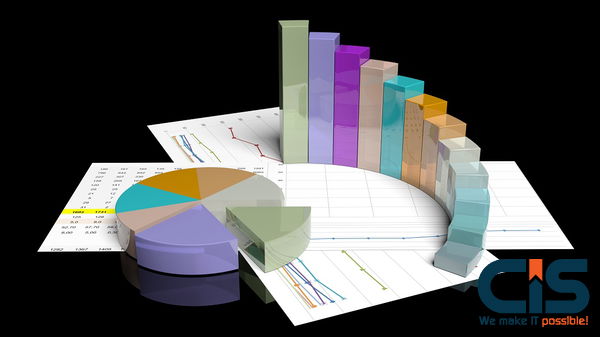
Achieving operational excellence requires a holistic strategy integrating technology, people, and processes. Here are some steps you can take to achieve operational excellence.
Aligning the Supply Chain Strategy to Business Strategy: A supply chain strategy aligned with business goals and objectives should be developed. This alignment ensures the supply chain operations focus on delivering value for customers and supporting the organization's strategic goals.
Streamlining processes: This includes identifying and eliminating waste, inefficiencies, and bottlenecks in the supply chain. Implementing lean principles such as Just-in-Time, 5S methodology, and Kanban to optimize inventory, reduce lead times, and improve flow is part of this.
Adopting Technologies: Adopting technologies such as Enterprise Resource Planning Systems (ERP), Warehouse Management Systems, Transportation Management Systems, and the Internet of Things can automate supply chain processes and improve visibility.
Building Cultures of Continuous Improvement: Continuous improvements involve a commitment to process improvement, learning, and innovation. It consists of setting up performance measures, conducting regular reviews, and implementing a continual improvement process to achieve operational excellence. Download free e-book, Expert Strategies for Implementing a Continuous Process Improvement Program, for more information about continuous improvement.
Implementing A Program Of Operational Excellence
A structured and systematic approach is required to implement an operational excellence program. Following are a few steps organizations can take to implement a functional quality program successfully:
- Define a vision for the organization and its strategy to achieve operational excellence: This is the first step. The program should identify the goals, the objectives, and the key performance indicators it will strive to achieve. All stakeholders should be informed of the vision and strategy to ensure alignment.
- Identify improvement areas: After establishing the vision and the strategy, the next step will be identifying areas in the organization that require improvement. A comprehensive assessment of an organization's systems, processes, and people can help to achieve this. The evaluation should identify areas of improvement and gaps that are aligned with the vision and strategy of the organization.
- Develop a plan of action: Based on its assessment, the organization should develop a plan of action that details the specific initiatives and projects required to realize the vision and strategies. The action plan must include KPIs, timelines, and responsibilities to measure and ensure accountability.
- Create a culture for continuous improvement: A culture of continual improvement is a critical component of operational excellence. This includes engaging employees at all levels, encouraging collaboration and communication, and empowering them to identify and implement improvement. Training and development can help develop the skills and abilities needed to create a culture of continual improvement.
- Implement the plan and monitor progress: The program should be implemented, and progress monitored by regular review of KPIs. The organization can then identify deviations from its schedule and take corrective actions.
- Recognize achievements and celebrate successes: Recognizing and celebrating successes is essential for keeping momentum and motivating employees. Recognizing individual and team contributions can help create a culture of continual improvement.
Following these steps, an organization can implement an operational excellence program to drive sustainable success and continual improvement. Operational excellence is a journey that requires the commitment and efforts of all stakeholders.
The Benefits Of Operational Excellence For Supply Chains
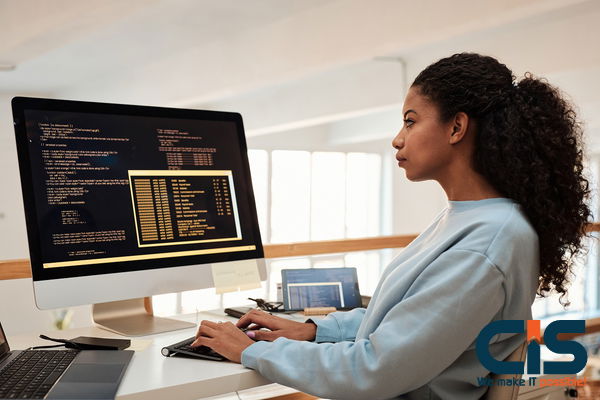
There are many benefits to achieving operational excellence in your supply chain.
- Cost savings: Operational Excellence helps reduce storage, transport, and inventory costs. This results in lower supply chain costs.
- Improved Service: Operational Excellence improves order accuracy and product quality. This leads to higher customer satisfaction.
- Competitive advantage: Operational Excellence gives organizations an edge by allowing them to react quickly to changing market conditions and customer demands.
- Improved Efficiency: Operational Excellence increases the efficiency of supply-chain operations. This results in increased productivity, quicker response times, and better resource usage.
Best Practices
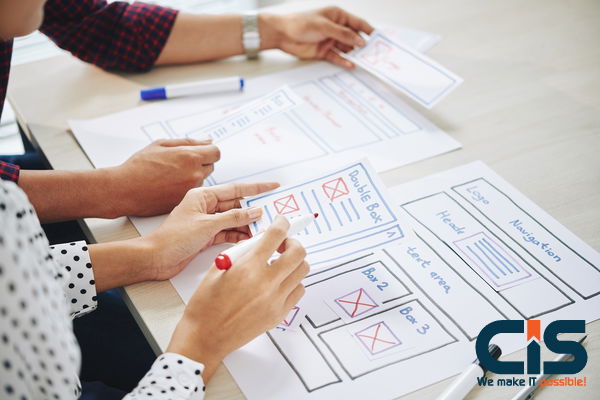
There are best practices organizations can follow to establish a program of operational excellence or to maintain it once achieved.
Following are some of the best practices:
- Standardization: Standardizing procedures and processes across the supply chain can improve consistency and reduce errors.
- Continuous improvement: Implementing an ongoing culture of continuous improvements helps to drive innovation, learning, and process optimization.
- Collaboration: Working with customers, suppliers, and other partners to enhance the performance of your supply chain.
- Data-Driven Decision Making: Using data analytics and insights, you can make better decisions and identify areas for improvement.
These best practices are guidelines that help an organization create a solid foundation for continual improvement when establishing an operational excellence program. You can achieve sustained success and continual improvement by integrating them into a functional improvement program.
These best practices will also help organizations maintain operational excellence once they have achieved it, as they allow them to continuously identify improvements, optimize their operations, and carry their competitive edge.
Digital Transformation for Operational Excellence
Digital transformation can significantly impact operational excellence programs since it offers new opportunities for organizations to optimize their operations and achieve more significant productivity, efficiency, and agility levels.
Digital transformation can have a positive impact on operational excellence programs.
- Process automation: The digital transformation allows organizations to automate processes. This can reduce human error rates and accelerate operations. Automation frees resources and will enable employees to concentrate on more valuable activities that require creativity and human decision-making.
- Data Analysis: Through digital transformation, organizations with access to large amounts of data can gain greater insight into their business. With the help of analytics tools, companies can identify areas of improvement and inefficiencies and make data-driven decisions to optimize their operations.
- Communication and Collaboration: Digital Transformation provides new opportunities for communication and collaboration among company parts and external partners. Collaboration tools, such as messaging platforms, project management software, video conferencing, and other collaboration tools, can help to facilitate communication between employees, customers, and suppliers.
- Agility: Increases an organization's flexibility by enabling it to respond quickly to changing market conditions or customer demands. Organizations can adapt rapidly to evolving needs by using real-time analytics and data.
- Customer experience: Enhance the customer's experience by offering new ways to interact with a company, such as mobile apps or portals. Organizations can increase customer loyalty by providing seamless, personalized experiences.
Operational excellence has a significant impact on the culture of an organization. Organizations that place a high priority on operational excellence cultivate a culture of collaboration, innovation, and continuous improvement. This culture encourages workers to be critical, look for new opportunities, and own their work. Operational excellence is embedded into an organization's DNA, resulting in sustained success and a competitive edge.
Five Ways To Improve Your Procurement Process
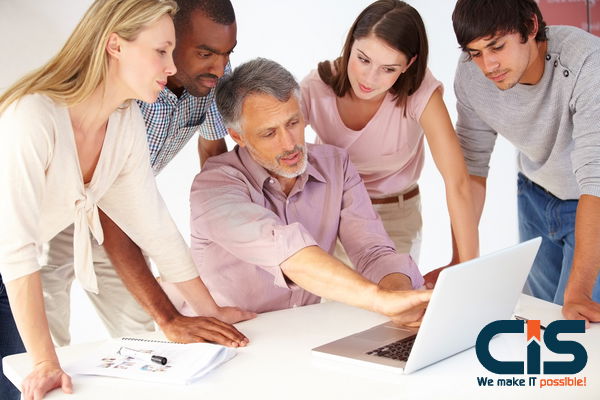
Assuring the efficiency of your procurement process can have a substantial positive effect on your organization. A world-class procurement organization goes far beyond fulfilling internal needs by purchasing goods and services to create significant business value. A successful procurement process should maximize all parts to generate substantial long-term savings for an organization.
You can use various methods to enhance your procurement process, from minor tweaks that target specific parts of the process (like creating internal documentation) to major modifications that transform it entirely. Here are a few ideas for adding value to the procurement process.
Implementing a Contract Management System
Implementing contract management software will save time and improve efficiency for any business. Drafting contracts can be time-consuming because many organizations deal with hundreds or thousands of vendors annually. Implementing such a system allows you to save yourself the trouble of writing new ones every time someone new comes along; instead, with this system, you can reuse existing contracts between vendors or create standard templates that only require minor alterations each time they're used.
Enhancing employee capabilities through training and development remains among the cornerstones of a successful enterprise, both from an employee's personal growth standpoint and to improve organizational productivity and profitability. Exercise benefits individual employees' personal development and contributes to organizational productivity and profitability by maintaining or gaining competitive advantages and increasing employee satisfaction while simultaneously cutting costs and speeding growth. Leading procurement organizations have increasingly adopted innovative training solutions - for instance, eLearning combined with simulations, which allow employees to immediately apply what they've learned to their jobs, ultimately leading them to make smarter decisions improving overall productivity through increased employee decision-making capacity.
Maintain Good Supplier Relationships.
Procurement professionals must surround themselves with happy and qualified suppliers when undertaking procurement activities. Placing out requests for bids may take longer to obtain definitive recommendations than anticipated, which will take away valuable time when it comes time for buying services or products from new vendors. Researching each new vendor, understanding their position within an industry, and identifying negotiation strategies can be time-consuming and expensive; to make life simpler, it would be much better to maintain relationships with a handful of reliable suppliers instead. Streamlining procurement will streamline the process and simplify your job while improving your reputation among suppliers who find you easy to work with - which could open up new sourcing avenues. Just ensure fair dealings between yourself and suppliers, timely payment of invoices, and clear and detailed RFPs are issued.
Reduce Expenses
Procurement professionals are valued for reducing costs while still meeting business needs while procuring products and services they depend on. But how? Careful consideration before each purchase must be given due respect - though this may sound easy enough, procurement professionals know it's easy to be lured into placing assets quickly in response to every request, leading to additional expenditure. Spend time researching products that you depend on in your company instead.
Analytical And Negotiation Skills
An expert procurement specialist must possess outstanding analytical abilities. Planning and executing projects, negotiating with vendors, and dealing with multiple suppliers require her to perform at her best. Skills learned throughout the procurement process should be put to good use throughout the procurement process to obtain maximum benefit from them. For instance, deep knowledge of quantitative data is vital for making sound financial decisions for your business, and negotiation requires practiced hands to master effectively. Finding a balance between negotiating the best deal possible for your company while building strong relationships with suppliers can be a difficult challenge, which is why advanced training and simulation are invaluable ways to develop negotiation skills.
The Conclusion Of The Article Is:
Operational Excellence refers to achieving maximum efficiency and effectiveness when managing resources, systems, processes, and other factors to deliver client goods and services. It involves optimizing operations within an organization to reduce waste, improve efficiency, and increase quality - creating lean, agile organizations capable of quickly adapting to changes in customer demand, market conditions, and industry trends - in short, creating Operational Excellence is not about attaining perfection - instead, it is a journey toward model rather than one definitive achievement rest api servicenow.
Operational excellence is the ultimate aim of supply chain operations. This term refers to managing resources and processes most efficiently and cost-effectively to meet customer demands while upholding quality.