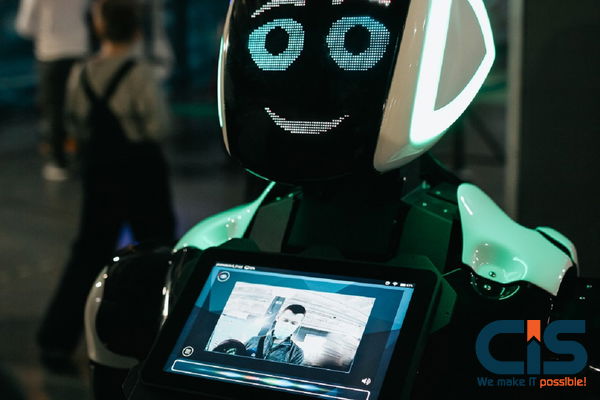
To do this successfully, it's crucial that your processes become standardized and that a quality management program (QM) be established and adhered to. Quality assurance (QA), or product/service testing, focuses on maintaining an expected standard in every production or delivery step to prevent errors from arising. It involves inspecting each step for potential mistakes during each stage.
Quality assurance (QA) can make or break a project's success, with stakeholder rejection due to product or service quality failing to meet expectations being an unacceptable outcome for project managers and stakeholders alike. So let's define this term further!
What Is Quality Assurance (QA)?
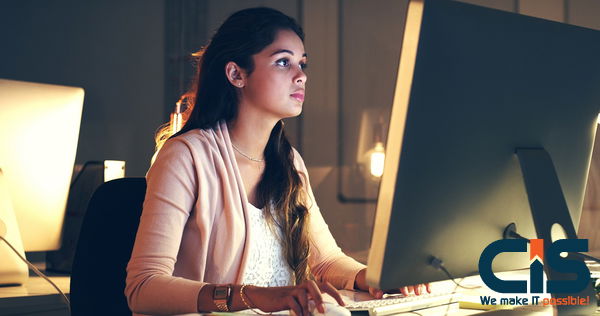
Quality assurance (QA) is a fundamental aspect of quality management that involves creating guidelines, standards and procedures designed to prevent issues with product/service quality and ensure integrity throughout the development process.
Quality assurance (QA) can sometimes be confused with a quality control system (QCS). A quality management system refers to an integrated set of basic tools and methodologies which enables organizations to effectively oversee all aspects of quality, including planning for quality, assuring quality, controlling quality and improving it over time.
Quality assurance (QA), also referred to as the Quality Control process, seeks to ensure a service or quality product meets a certain standard and is free from defects at each step of production or delivery. Achieving excellence at any company level is crucial, which makes quality assurance programs essential. By helping businesses identify areas they excel in as well as those where quality improvements should be made, they can reduce errors that might otherwise incur costs over time and minimize costly errors altogether.
Note that quality assurance (QA) differs from quality control (QC). While QA aims to prevent defects from happening, QC detects them. A QA plan differs from its counterpart, but there may be overlaps in planning processes between both entities.
Want More Information About Our Services? Talk to Our Consultants!
History Of Quality Assurance
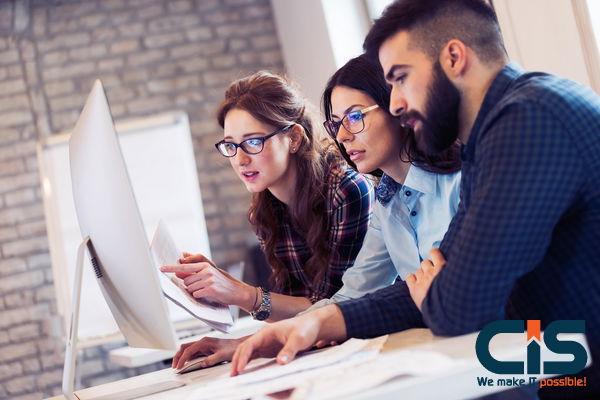
Quality standards are nothing new: guilds employed them during the Middle Ages to uphold quality in goods and services provided to members, establishing them as conditions of membership. Royalty was responsible for overseeing their warships' upkeep. Furthermore, royals helped standardize training practices to make long sea voyages safer than before.
Quality assurance was revolutionized during the Industrial Revolution. No longer did workers solely bear responsibility for assuring quality in their work; supervisors, management teams, and special groups were put in place to oversee it all.
Using A Quality Assurance Plan
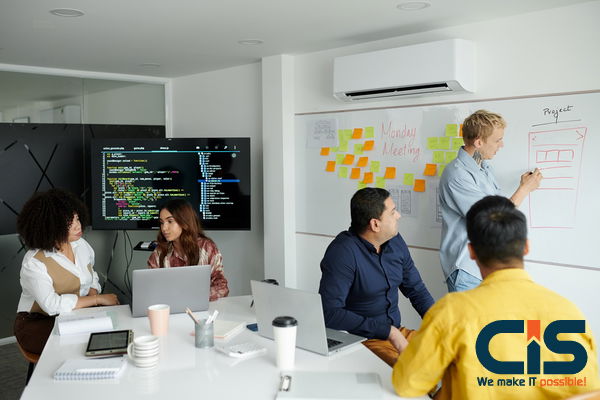
No matter the size or nature of your company, procedures must be implemented that ensure product management-simply having an idea and then immediately selling it without first conducting research are not good solutions for success.
Products and services must deliver value for customers who purchase them, which can only be accomplished with an effective quality assurance plan that ensures quality conforms with both end users' specifications and industry requirements. A quality plan helps prevent errors from surfacing while pinpointing areas for further advancement.
A quality control plan addresses every facet of product/project development, such as its functions and how they're carried out, its maintenance, or any changes needed should they arise. Quality assurance templates allow companies to tailor the QAP according to the specific needs of their company, such as software or product quality assurance, or focus on growth or customer service, respectively. Quality control is the process of testing the final product after it has been produced.
Principles Of Quality Assurance
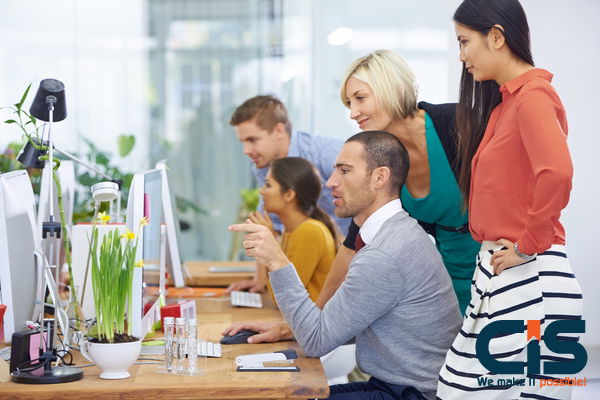
Quality assurance relies on two fundamental tenets. First is "fit-for-purpose", whereby products must meet their intended use without exception. At the same time, "right the first time", in which any errors are immediately rectified.
Project management strives to ensure the service or product being offered operates flawlessly at all times, and quality assurance processes include managing raw materials and assemblies; products, components and services; as well as production management and inspection processes.
Quality Assurance Methods
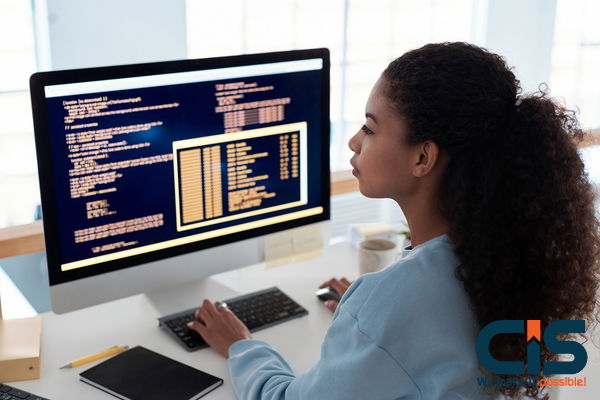
Quality Assurance (QA) plays an essential role in product creation and manufacturing. Quality control methods have evolved throughout time; you can select one suitable to you by studying this list.
Total Quality Management
Total Quality Management (TQM) is an approach to quality assurance that involves creating an overall corporate mindset toward quality assurance. All departments and employees involved with activities affecting quality standards (like inventory or supply chain management ) will receive training on maintaining these standards.
Failure Testing
Push testing is an effortless method of quality assurance that involves subjecting products to extreme environments - pressure, temperature or tension - in order to reveal any product defects that have yet to be detected by other means of quality assessment or improvement efforts. Real-time Data collection occurs throughout this entire process to facilitate quality assurance and product continuous improvement efforts.
Process And Product Quality Assurance
Quality assurance methodology centers around creating procedures and standards at the organizational level to evaluate, measure and resolve quality issues. It relies heavily on an in-depth gap analysis for different business processes involved with quality management.
Capability Maturity Model Integration
Capability Maturity Model Integration (CMMI) is an increasingly popular approach in software development. CMMI assesses your company's maturity when it comes to quality assurance, and development teams must learn all stages of CMMI until achieving an efficient quality assurance system.
Statistical Process Control
Quality assurance involves using statistical project management tools to measure, identify and assess the quality of processes, project teams and business operations - ultimately leading to improved production cycles by eliminating flaws within.
Quality Assurance Responsibilities And Roles
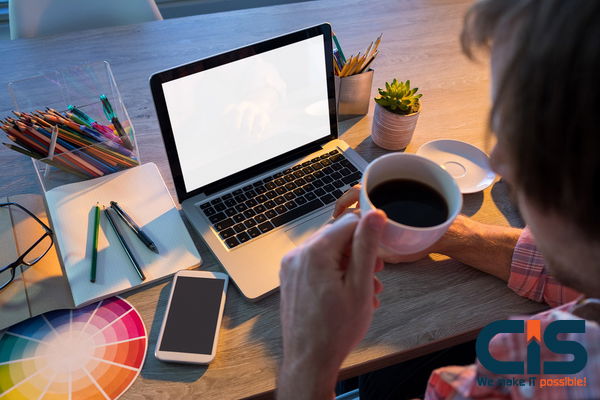
Teamwork is the key to achieving quality assurance. When it comes to QA, there are two main roles and responsibilities.
Quality Assurance Specialist
As the name suggests, a quality assurance specialist oversees the QA component of quality management. The quality manager collaborates with them to achieve strategic alignment.
Quality Manager
An individual manager oversees all aspects of quality management systems. Working closely with their team members, this individual ensures alignment of quality assurance with the strategic goals of an organization while overseeing quality control, improvement, and planning initiatives.
Quality assurance systems help create objectives for services or products of projects by measuring them against predefined standards, monitoring production processes to detect any mistakes in production, providing feedback as required and providing oversight feedback to ensure no mishaps take place. Quality control, however, generally only looks at the output of processes.
Which Industries Can Benefit From Quality Assurance?
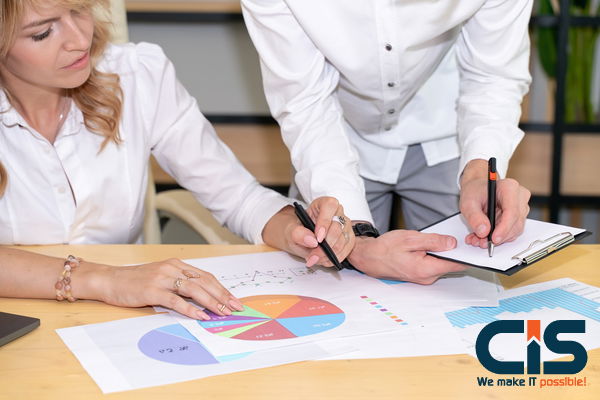
It is not uncommon for contractors and consultants to be hired by industries to ensure quality.
Medical Industry
Quality assurance in medicine is of vital importance; one misstep could result in death for a patient. Agencies used across laboratories and hospitals ensure their standards match those set forth by industry regulations.
Aerospace Industry
Quality assurance in the aerospace industry is known as product assurance. It works together with quality engineering and project management to prevent catastrophic failures. Product assurance reports directly to senior management with its budget allocation.
Software Industry
Quality assurance in software engineering is an indispensable way to oversee its processes, from ISO 9000 certification through Capability Model Integrity (CMMI) models to using software patches to resolve problems. Quality Assurance software may even be employed directly as part of this practice.
Read More: Implementing A Technology Services Quality Assurance Program
What Is The Purpose Of A Quality Assurance Management Program?
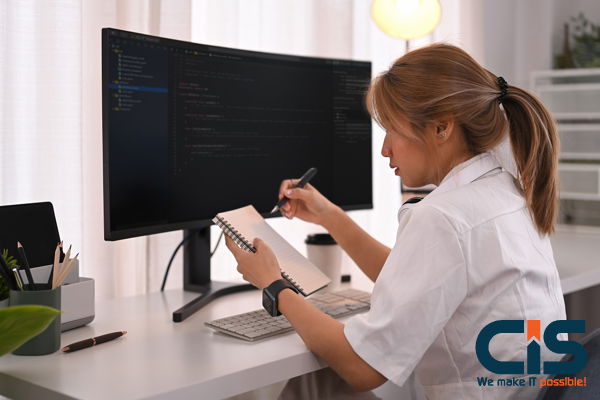
Future contact centers will focus more on quality management. It would be best if you implemented more robust processes for dispute resolution, coaching, evaluation and calibration. Your program must address all three levels of quality management: tactical, operational and strategic. Utilizing our methods, you will be able to target operational levels as you implement change on tactical and strategic organizational levels.
An effective quality management program can assist your company in reducing noncompliance, mitigating mistakes that arise during customer interactions, and mitigating other internal errors. Standardized processes provide an organized work environment, helping contact center employees focus their energies on performing their duties more efficiently.
A superior process of quality management may enhance customer satisfaction and build customer loyalty. How difficult is it to develop a program for quality management? No! With the proper strategy in place and these eight steps as guides, this important task should be achieved without difficulty.
Set Standards And Goals For Your Customer Service
Imagine what results your contact center team would like to achieve and the steps needed for improvement, then decide the direction in which to build agent QM programs. This helps outline where to direct efforts when building agent quality programs. Start by considering who your ideal customer is. Doing this can help set goals for quality:
- What are the desired outcomes for your clients?
- How do you want your customers to feel about the service they receive?
- What should be the overall impact of each interaction with a contact center on customer satisfaction?
- How important is customer service in fostering customer loyalty?
- What should the customer feel after they have finished the live chat (or other digital interaction) or ended their call?
- What do you want the participants to say or do after their interaction with them?
- What do you hope customers will think of your brand after contacting customer service?
Consider how your staff will assist your desired outcomes to clients to enhance service quality when creating your program for quality management. As part of that effort, it's also crucial that agents act accordingly so they can reach those desired goals.
Establish clear goals to guide the evolution of your customer service team over real time. Be transparent when setting standards. What metrics (First Contact Resolution, Service Level etc.) will you measure, as well as their acceptable results? Often these measurements can be found within performance scorecards alongside more traditional quality measures.
Once you've addressed all the details surrounding quality, set standards for each aspect of your work and outline clear goals that your agents strive towards reaching. Please don't be shy to offer constructive criticism as their journey continues toward accomplishing these quality targets.
Establish Policies And Procedures For Each Department
To achieve quality within your company, all members should participate. Develop customized procedures tailored for every level and department, so all staff can actively contribute towards developing the new quality policy.
Quality policies should establish expectations regarding attendance, overtime work and behavior at work. Procedures should encompass every element, from how agents will interact with customers to when and how feedback may be expected - remember your quality metrics here!
If your company doesn't already have one, consider creating one as soon as your policies and procedures have been finalized; once in this document, they'll be easily accessible by your team in one central repository.
Share The News
Once your quality plan has been developed and its details outlined in your quality manual, be sure to inform employees about any new requirements or procedures related to quality. Before making this announcement public, discuss implementation with department experienced leaders first and discuss potential impact before going public with any announcements.
By engaging your managers, you can prepare them for any changes that lie ahead while giving them time to train frontline staff and answer any queries from employees. An effective launch is vital to maintaining long-term quality plans and levels.
Your team should be well informed of your Quality Management Plan (QM Plan) and ready to answer any queries. However, depending on how significant changes will be to some quality goals, only a manager might need to discuss the reasoning for them with each employee individually.
As this will be the inaugural official contact center quality-management program, take extra real time and care in explaining it to all employees or the entire staff. Arranging work sessions or staff meetings would help.
Tell them why these efforts exist by starting from an overall concept. Focus on discussing how quality assurance (QA) meets customers' expectations and ensures customer satisfaction; be ready to discuss major quality expectations moving forward as part of this discussion. To have an effective quality management initiative (and increase customer loyalty), all members of your organization need to participate.
Follow The Procedures
Now the fun can start! Work closely with various department heads to put new policies into action through training for agents, individual meetings and constant employee feedback. At first, some doubts may arise. While all parties involved share a long-term goal of building customer loyalty, questions regarding quality plans might initially arise. Your job then should be to address all questions or voice any concerns from both frontline workers and managers alike.
Regular tracking and reporting will help to ensure compliance with any new procedure; quality management solutions play a vital role here. Establish a date and time for transitioning between old and new quality management systems, remind your staff in advance, and announce it during an early work shift to ensure everyone understands this new program is starting off on an even note.
Managers may need to remind agents in the early days of implementing the plan if they need help. Once again, solutions for quality management can make an enormous impact; this experience provides all parties involved a chance for growth.
At first customer interactions, even after extensive training has taken place, new staff may fall back into old patterns of interaction and fall below your standards. It would be best if you remained patient yet insistent upon meeting them. Though you may wish for immediate increases in customer satisfaction levels, development must take time. Patience must be exercised as part of this process.
Now is the time to put your quality control plan into action, by training all employees on its contents and equipping your team with the necessary resources and quality tools for meeting its goals. Your Quality Assurance Plan must also be easy for production and HR personnel to follow and understand, meeting risk management guidelines. Lastly, confirm with production that it adheres to relevant documents for risk mitigation.
Receive Feedback
Organize a discussion session and solicit feedback from managers shortly after you've implemented quality standards, then have them meet with their teams to share what experience they had with the QM program. By encouraging 360 deg feedback, you're giving everyone in your organization an equal chance to contribute towards improving its quality.
As you work to refine your QM plan, take an approach-focused approach in meetings. Don't use these sessions as an avenue for managers to vent or express frustration; provide them with an open forum to voice any worries and discuss possible concerns or raise any issues they might be experiencing. Remind everyone how quality management can revolutionize how customer quality expectations are met.
Keep the goals of customer satisfaction, quality standards and loyalty top of mind over time with your quality management scorecards to help refocus everyone on the goals of the business. No need to panic if comments or queries emerge that need further examination; that is perfectly okay. These feedback sessions exist solely to explore internal processes rather than provide solutions.
Consider your Quality Assurance Plan as a living document that can change and adapt as required by your team. While its initial objective should remain at the forefront of everyone's mind, its main use lies in meeting team goals more effectively - why and how will new guidelines or policies assist this effort? Listen closely to your teammates, customers and other employees so you meet realistic expectations set before them.
Read More: The Value of Quality Assurance in the Custom Software Development
Measure Results
Analyze and evaluate agent performance, customer satisfaction levels and feedback to ascertain which processes have seen improvements over time. Customer interactions must be reviewed as part of these audits, as KPIs must also be examined for any meaningful change to occur.
Check that the goals you established when developing your QM program have been achieved and evaluate other results which had previously been exceptional before making changes to be certain you have enhanced team quality without altering existing successes. Doing this will give you peace of mind that any positive outcomes have not been diminished due to changes.
Communication Of Results
Staff motivation can only increase with evidence that their work has made tangible differences within a business, so regular reporting of your results will keep commitment alive in staff members and frontline workers alike. Frontline employees directly contribute to customer satisfaction increases and loyalty boosts through customer interactions they directly impact.
Be sure to inform employees how their contribution has affected the success of their company. Your staff helped create new standards of quality and operational procedures; motivating and empowering your staff will help them embrace and achieve your vision for their organization.
Reinforcing the message further by rewarding those who adhere to your plan with outstanding results will strengthen it even more. Achieving positive outcomes is of key importance both to you and to customers; make sure your team follows it without needing feedback; reward compliance regardless of results.
Verify with agents and managers what changes have taken effect, clarify any confusion over quality management with them individually, as well as discuss any misconceptions concerning it with managers directly.
Just Adjust As Needed
Your Quality Management (QM) policy and procedures were originally all theoretical. Once customers provide feedback about quality processes and results are quantifiable, then it's time to identify any gaps or improve procedures by increasing customer feedback, improving training or analyzing their experience with them.
Organize a meeting with your employees to discuss ways you can increase employee performance and meet customer service goals. Adjust any business standards which don't work in the quality control department and inform the manager if there is anything additional you do not wish to modify; failing this, managers could become confused as you fail to explain details of the quality control program in detail.
Add the updated policies to any digital or printed document containing SOPs, such as an official manual of formal SOPs or just rules for quality control. Assign a quality control team who will report back concerns from different departments.
After carefully considering feedback from stakeholders and clients, make adjustments as required and consider making plan reviews every two or three months, but earlier if necessary. When any problems or flaws have been identified, adjustments must be implemented quickly if they want your company's goals and sales revenue goals to be reached on project schedule.
Want More Information About Our Services? Talk to Our Consultants!
Conclusion
Your customer service might be working effectively now, but that doesn't guarantee its continued success in the future. Receive regular feedback. Measure and communicate results. Adjust as necessary on an ongoing basis- this should happen once or twice each year to stay abreast of ever-evolving and dynamic trends in customer service while upholding high-standards quality management programs.
Even if your goals remain the same for your team, advances in technology and industry could alter how tasks must be accomplished daily. Following these steps can help create an updated quality management program to keep goals flexible while keeping teams on the right path regardless of any changes that might come about.