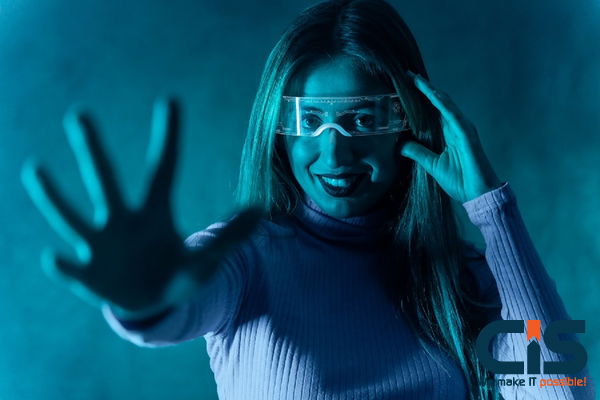
What Is Code Quality: Overview + Method to Enhance It
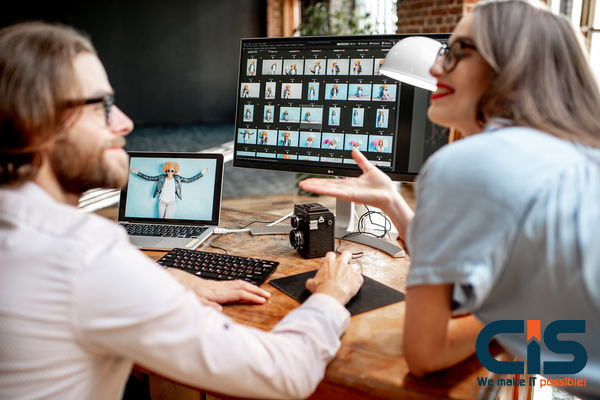
Code quality metrics define code as either good (high-quality) or poor quality (low-quality), with terms for both being subjective. Different teams use various terms when discussing code quality: for automotive programmers, it could mean something completely different, versus Web application developers define high quality differently; we explain code quality itself along with ways of improving code quality, important metrics related to it, as well as tools available for improving it.
Your choice: read along or jump ahead directly to an area that catches your interest.
- The importance of code quality
- What is the best way to measure code quality?
- What is the best way to improve code quality?
- Start with Code Quality Analysis.
Why Code Quality Matters
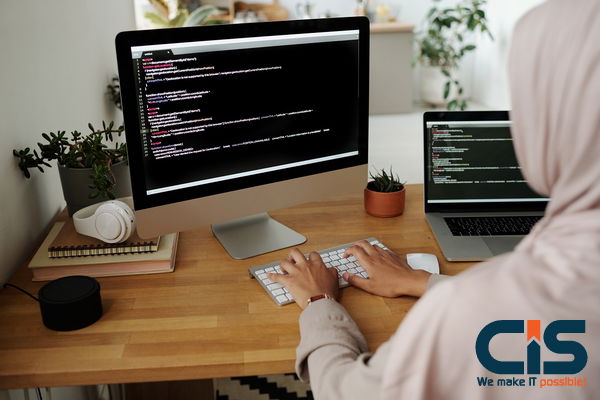
Software quality has an enormous effect on overall software quality; quality also affects the safety, security, and reliability of codebases. Many teams today strive for high quality when building safety-critical products - it becomes even more essential.
Code Quality Analysis: What Defines Good vs Bad Code
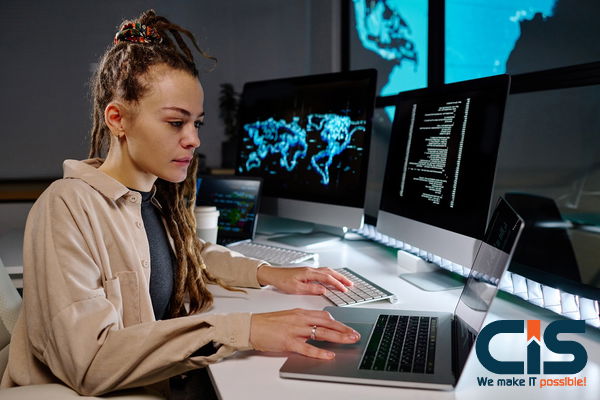
High-quality code refers to code which has passed the test of time; clean code can often indicate high-quality writing; low-quality code is usually indicative of inferior work that won't stand the test of time, while good codes include these characteristics:
- What it says.
- Has a consistent style.
- Easy to understand
- Documentation is available.
- You can test it.
Tests Aren't Enough
Programmers don't always meet our expectations when it comes to code reviews and testing; therefore, not all errors will be detected through reviews and testing methods alone. A study entitled "Software Defect Origins and Removal Methods" found that programmers were less than half as effective at finding bugs within their code than testing companies - with most forms only managing around a 35% efficiency rating. As it's hard to measure quality accurately, it becomes hard to assess quality in an assessment context.
Code Errors Can Lead To Risk
Code errors can present serious risks. It is vitally important when programming to pay close attention to the quality of code; any lower quality can pose security or safety threats and lead to catastrophic results in software malfunctions.
Everybody Is Responsible For The Quality
Quality responsibility lies with everyone--developers, testers and the end customer alike. Aiming for high standards throughout development should always be our objective.
Want More Information About Our Services? Talk to Our Consultants!
What Are The Metrics For Measuring Code Quality? Measure Code Quality
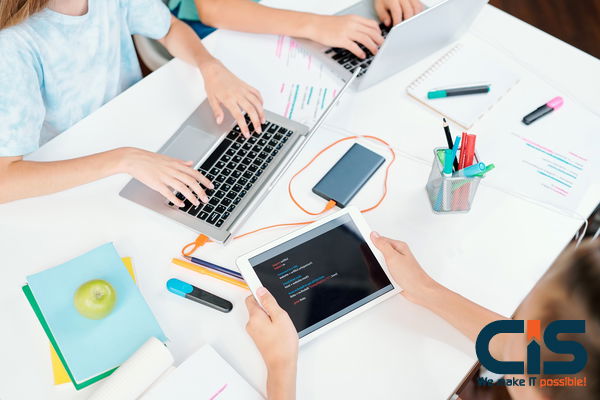
Unfortunately, you cannot use just one method of judging code quality; your team might measure different characteristics than other teams do.
Key Aspects of Code Quality to Consider
Here are five aspects to look out for when assessing code quality.
Reliability
System reliability can be measured as the likelihood that it will operate error-free for an agreed period, including availability and several software defects. A static analysis tool can measure defects, while the mean time between failures (MTBF) can measure software availability; both measurements provide insight into developing an error-free codebase. A low defect count is essential in developing robust code.
Maintenance
Software maintainability can be defined as how easy updates can be made to existing codebases, including size, consistency and structure factors that directly influence it. As well as these three considerations, maintainable code depends on other aspects, such as understandability and testability, for optimal functioning.
Maintainability cannot be assessed with just one metric; you can increase maintainability by monitoring style warnings and Halstead Complexity measures, among other metrics. Maintainable code bases require both automated and human reviewers.
Testability
Software testability is an indicator of its compatibility with testing processes, measuring how effectively a program complies with them. Factors influencing testability may include how easily software programs can be controlled, observed, isolated and automated for automated testing purposes; how easily potential flaws can be discovered via tests performed against them and their size or complexity being factored in, while code-level methods like cyclomatic difficulty help enhance it further.
Portability of Device
Software ports in different environments are measured for portability; this relates to platform independence. While portability cannot be measured directly, there are multiple methods you can take to make sure your code remains portable: testing on multiple platforms regularly rather than waiting until all development work has been finished; increasing compiler warning levels accordingly and using two compilers; as well as setting and adhering to coding standards as part of any standardization effort.
Reusability
Reusability refers to whether assets, such as existing code, can be reused again in different forms or situations. Modularity and loose coupling are two characteristics which increase reuse. One way of measuring reusability is the number of dependencies; you can identify interdependencies by running static analysis tools.
Imagine producing products of consistently high quality from their very first production run onward. Quality assurance and control measures can assist you in meeting this goal; such measures help detect mistakes before they arise and correct those which do occur to ensure happy customers and healthy profits for you.
Quality assurance (QA) seeks to prevent defects from appearing in products and services. In contrast, quality control (QC) entails inspecting them to verify the accuracy of specifications. Together QA and QC ensure customer expectations are fulfilled through what you offer them. This dynamic duo of techniques should help your production run more smoothly.
These terms are often used interchangeably; however, there are key distinctions. Here's everything you need to know about quality assurance and control. We have also provided you with a complimentary checklist which can assist in the implementation process for both processes.
Quality Assurance Vs Quality Control
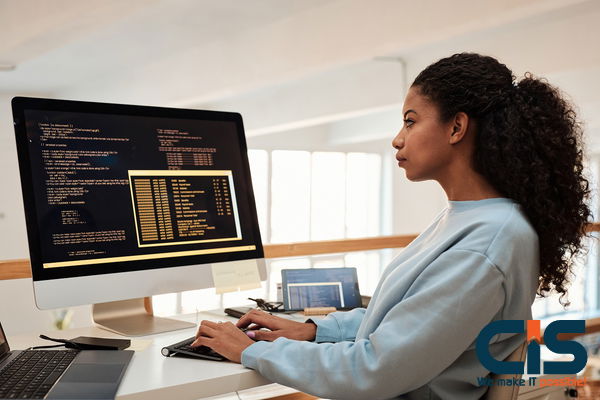
Quality Assurance & Control
Quality management encompasses various concepts related to quality assurance (QA) and quality control (QC), which together comprise quality management activities required to reach and sustain excellence levels. Both practices work hand in hand towards satisfying customers' expectations for quality, while each has a particular emphasis.
Quality Assurance
Businesses trust in Quality Assurance to fulfill product promises efficiently and effectively, which involves monitoring production to detect errors and enhance manufacturing processes while selecting development/testing techniques to make sure production teams use appropriate processes at appropriate times. QA provides oversight in these efforts by monitoring production to prevent errors while increasing process efficiencies.
Quality Assurance (QA) plays an essential role in helping workers meet quality objectives for every product or service produced or provided, from goods and services to human beings themselves. Understanding what it takes to reach quality and then creating systems to reach it is the essence of what QA stands for; quality control managers play a pivotal part when developing new products. Quality Assurance (QA) is responsible for setting production-related standards and protocols through testing.
QA managers utilize feedback provided by their QC teams. When any defects are noticed by these departments, QA teams use this as feedback to develop strategies to prevent it from happening again in future production runs. Furthermore, many production processes rely on optimizing processes, so errors will not arise regardless of whether an inspection was performed before delivery; sometimes, sampling techniques must be applied instead, leaving items without scrutiny until later review by inspectors.
Quality assurance covers all bases to guarantee production is of a high standard, from product specifications and requirements through production execution and evaluation to testing procedures, with various roles within quality assurance teams facilitating these procedures and following established protocols.
Quality Control
Quality control refers to the practice of designing, manufacturing, marketing, servicing and promoting goods and services which meet customers' satisfaction while remaining cost-effective and worthwhile for them to purchase. Quality control involves inspecting products to ensure they comply with quality standards, using various methodologies and processes to identify whether data from products conform with such criteria.
Testing units carry out Quality Control to make sure their product satisfies all required end-product criteria. Before products reach customers, workers in Quality Control verify if they meet standards set during development and testing; should any product fall below standards, then the Quality Assurance team is alerted immediately so it can analyze any defects, give feedback to the operations team, implement processes to eliminate error recurrence as quickly as possible and put processes into effect to stop future errors from reoccurring - ultimately creating an environment in which both managerial Quality personnel and operational staff strive for perfection together.
QC requires businesses to create environments in which both managerial QA personnel as well as operational staff strive towards perfection together - an environment which strives towards perfection by all involved - both managerial QA personnel, as well as operational staff, must strive towards reaching perfection together.
Read More: The Value of Quality Assurance in the Custom Software Development
Quality Assurance Vs Quality Control
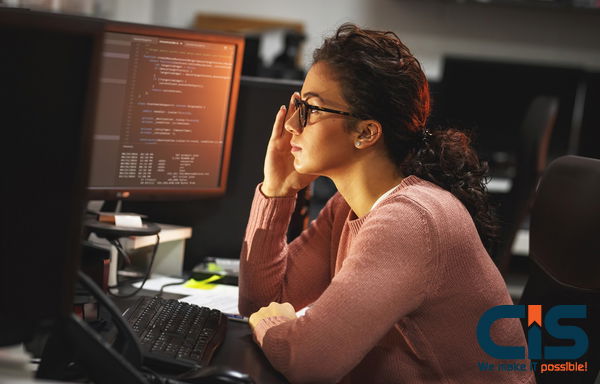
The terms quality assurance and control are often used interchangeably since their characteristics overlap significantly; however, they're distinct in some important respects; although both stem from similar roots, there can be key distinctions. In this chapter, we'll outline those distinctions further.
Proactive Versus Reactive
Quality Assurance (QA) teams take a proactive versus reactive approach when meeting customer requirements; in contrast, Quality Control teams offer feedback regarding how the final product could be improved upon based on what QC can inspect for quality issues during production processes and give regular quality evaluation reports back. Together they enable continuous quality improvement.
QA Processes focus on Preventing Defects through Process Design. With input and improvement from their Quality Control (QC) teams, the aim is to resolve errors without repeating them permanently. In essence, quality teams want no defects whatsoever in final products, so they work tirelessly at eliminating these through audits and quality adherence documentation.
Expecting defects to arise and promptly rectifying them as soon as they do is what quality control does best while being informed about what improvements need to be implemented, makes quality control proactive in its approach and, should standards not meet expectations, implement corrective actions quickly before reporting deficiencies to QA for review.
Product vs Process
Quality Assurance (QA) aims at increasing actions and processes used in creating the product. At the same time, Quality Control (QC) teams focus on producing top-quality goods. When problems are detected with products, they apply short-term fixes. QC teams may identify these immediately for a report back to the Quality Assurance department for long-term improvements; problems reported from this QA department go through long-term fixes while immediately detected ones go straight through to their department (QA for optimal processes to prevent future errors; while Quality Control works to detect and solve them immediately).
Data Creation Vs Verification
Before and during data collection, quality analysis (QA) must be used. Activities beginning during planning should begin before any work on new product production starts. QC begins once production has ended, as it ensures compliance with quality standards by monitoring finished goods against expectations.
Long vs Short-Term
Quality Assurance doesn't represent one specific phase in development. Rather, it represents a continuous effort to assure, implement and enforce quality. Most often, it focuses on long-term process improvement measures over the lifespan of product creation. The process for quality assurance typically lasts at least several years beyond product creation itself.
Quality control (QC), on the other hand, is typically conducted as the final phase in production. A team dedicated to quality assurance commences work once they gain access to the finished product from production; their work concludes when delivered directly to the customer. QC's primary concern lies with providing customers with products of the highest possible quality; only then is delivering this outcome possible.
QA Goals vs QC Goals
QA's goal is to implement procedures and processes designed to minimize risk and avoid errors from occurring, while Quality Control's objective is to guarantee final products meet company-defined quality standards.
Quality Assurance (QA) ensures quality, while Quality Control (QC) monitors that quality is delivered. Both have similar goals but take different approaches: QA establishes expectations while QC verifies they have been met, using iterative processes to minimize production errors; with one focused more heavily on processes while one on products.
Full Team Vs Full Team
Full Team Vs. The entire product development team plays an active role in quality assurance (QA). They ensure staff have all necessary skills, information, and materials needed to fulfill customer promises, outlining requirements for products as well as criteria that need to be fulfilled, with metrics used to monitor whether these criteria are fulfilled or not.
QC personnel are solely responsible for inspecting products to guarantee their quality, using criteria and metrics established by quality assurance (QA). Each product line needs at least one person dedicated to quality control (QC).
Comparing Quality Assessment Processes Quality Assurance and Quality
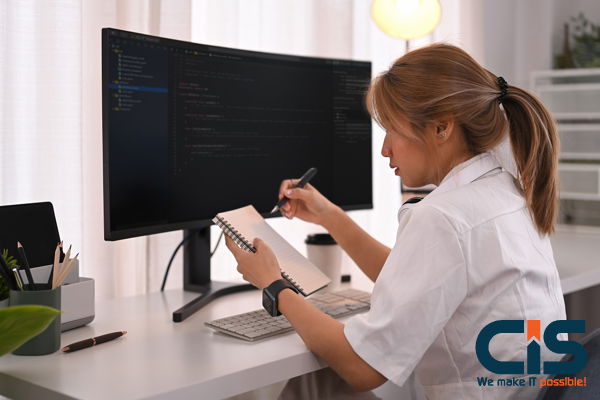
Control Teams (QA and QC teams, respectively) have unique goals, approaches, and focus when it comes to measuring quality. Both should work collaboratively if any quality improvement is to last beyond an immediate boost. In this chapter, we explore various measures QA and QC use when measuring quality.
Quality Assurance Processes
These quality assurance processes represent all actions undertaken by the QA team to guarantee quality. Below is an outline of these QA processes:
Documentation
Manufacturers record each step in their production processes in reports designed to address errors or issues which need correction, with suggestions as to how problems should be fixed quickly to minimize repeat occurrence.
Auditors
Quality assurance teams conduct audits at companies. Their purpose is to measure whether an organization abides by industry or business-specific principles and specifications - for instance, in a bakery where customers appreciate softly crusted loaves of bread, an auditing group will assess processes in place to meet that expectation consistently.
Trainees
Quality Assurance teams offer training to employees to maintain quality at every level. Both manual and automated testing techniques, and testing for different production environments, are covered. Teams should also identify and solve workflow issues related to production problems while adhering to standards and safety regulations, as well as document their activities through quality audits before creating operating or training manuals for employees.
Watching
Quality Assurance teams oversee production to ensure standards of quality are upheld during each production stage, ensuring workers adhere to industry safety and quality requirements while meeting production reliability benchmarks.
Quality Control Procedures
There are various approaches to quality control:
Inspection
Quality Control teams perform quality assurance (QA) inspections on products before their release into production, such as inspecting each quality against its standards during production and measuring and inspecting processes against specific requirements to determine compliance - this ensures quality materials throughout.
Inspections are carried out by:
- Sorting out defective from non-defective parts.
- Finding defects in raw materials or processes.
- Stopping further processing of spoiled semi-finished goods.
- Checking product design can help you detect the weak point and its cause.
Sample Product
Sampling involves selecting components randomly from many products for quality testing purposes. As it would be expensive and impractical to conduct quality control (QC) checks on every single one, random sampling provides the solution; its success indicates its overall quality as measured by how many randomly sampled units pass quality checks.
Laboratory Instrument Testing
Instruments are tested regularly in a lab environment to locate, correct and reduce defects on an instrument that has been serviced by qualified service staff. Tests usually run before each shift begins after these services have been provided to an instrument.
Quality Assurance Vs Quality Control
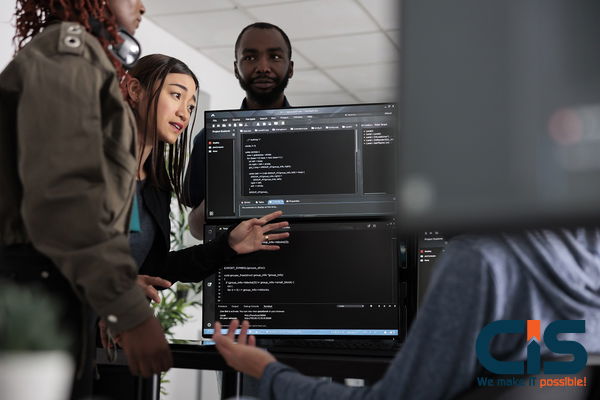
Each team in quality management plays its distinct part, yet must work cooperatively together. Quality Assurance teams seek to optimize processes while preventing repetitive long-term issues. In contrast, Quality Control (QC) teams address short-term concerns while giving feedback back to QA teams.
Quality Assurance Roles
The Group Quality Facilitator
A group quality facilitator brings quality ideas into their group while acting as its advocate. In contrast, quality managers oversee processes and standards for quality within a business goal.
Quality Assurance Manager
A quality assurance manager plays an essential role in developing and protecting quality standards in companies. They evaluate products to make sure they comply with company requirements while meeting customer standards for quality.
Quality assurance managers work to ensure the products their company creates meet specifications in terms of both production quality, safety and consistency of design.
Project Manager
Project managers are accountable for overseeing the successful creation and completion of any given project; its quality assurance and cost control, productivity enhancements and reliability assurance of products. In their role, they must maintain an optimal balance among costs, productivity and product reliability assurance - making important decisions regarding which issues need addressing quickly and in what order. They review reports to track projects as they move along successfully.
Quality Control Reviewer
A quality control reviewer or senior individual is responsible for reviewing milestone submissions before sending them out to clients. Quality control reviewers also verify products after each production stage to make sure that they meet customer demands; additionally, they record measurement changes so they can monitor improvement efforts over time.
Quality Control Roles
Members of the Quality Control Team are charged with carrying out these roles. Their performance plays an essential part in testing and inspecting finished goods, including raw materials, packaging materials, in-process materials and finished goods.
Designer
Designers create documents. A designer must develop specifications of quality standards expected for final products as well as prepare documents for inspection purposes. Designers also create efficient designs which can be applied across products within an organization.
Checker
Checkers are independent document reviewers who act as monitors to review designers' works to make sure that they adhere to industry standards and customer satisfaction levels, making corrections to documents when necessary, monitoring customer satisfaction levels and suggesting improvements to production processes.
Back Checker
Before updating, the back-checker verifies or rejects corrections made by the checker.
Updates
Updaters (also referred to as revisers or updaters) are responsible for updating documents as per an agreed revision schedule.
Rechecker
Rechecker, an independent software evaluation specialist, analyzes software products to detect any possible flaws and suggest enhancements for improvement.
Agents of Quality Control
Quality Control Officers Quality control officers conduct assessments on major products sent out and raw materials arriving. Furthermore, these officers review specifications that help understand product needs better.
Other roles played by actors:
- Returning materials and rejecting any products not meeting standards. Reporting their findings to a quality assurance team.
- Train the QA Team on how to improve your products and services.
- Testing and assessing products
- Reporting issues and recording them.
- Supporting Process Improvement
- Repairs are necessary.
Want More Information About Our Services? Talk to Our Consultants!
Conclusion
No quality management system would be complete without both quality assurance and control; they complement one another but have different focuses; for instance, QA tends to focus more on processes, while QC tends to prioritize products; also, one aids the other when dealing with errors whereas both will help your company reach higher quality levels overall. Using both will lead to superior outcomes. Your organization will benefit greatly from Cyber Infrastructure Inc.'s free documentation trial service and our helpful checklist on quality procedures implementation.