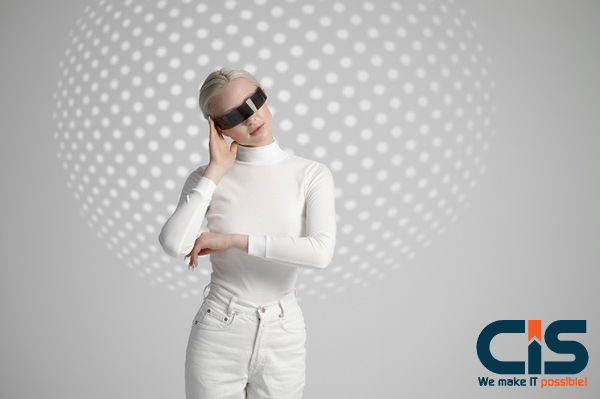
Manufacturers can monitor their operations in real-time by using vital Fourth Industrial Revolution (4IR) techniques like automated machine learning, sophisticated and advanced analytics, and IoT (Internet of Things). This allows them to collect huge quantities of operational information to:
-
Monitor key KPIs such as OEE production rate or scrap rate
-
Make sure you know the exact delivery date and ensure that you don't miss deadlines
-
Be aware of potential disruptions to the supply chain
-
Troubleshoot bottlenecks in production
-
Find and correct inefficiencies of equipment as and when they begin to develop
According to McKinsey according to McKinsey, the 4IR technologies could produce as much as $3.7 trillion by 2025. AI alone could create $1.2-$2 trillion worth of value in supply chain and manufacturing management.
Automated systems for intelligent manufacturing are facilitated through IoT devices, also known as the IIoT (Industrial Internet of Things), which allows for the growth and streamlining of every aspect of the business. Additionally, the use of technology of AI and robots is especially beneficial in the industrial sector since they can improve product quality, productivity, production efficiency, and overall performance.
The development of cobots or collaborative Robots is becoming more widespread in industries, lab work, and commerce. Cobots can take instruction from humans, allowing them to be more productive with them, including instructions that weren't originally thought of in the first programming. Robots aren't tired, hungry, or bored. They have capabilities that Artificial Intelligence is far beyond human capability in things like miniaturization and precision measurements. They offer a vastly superior quality of assurance.
Why AI is Critical to the Future of the Manufacturing World?
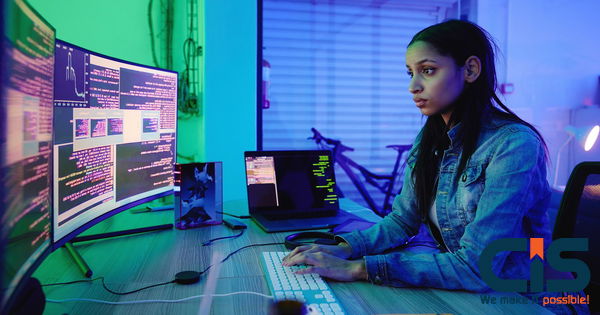
Every company aims to discover new ways to save money and earn money, lower risk, and increase the overall efficiency of production. This is vital to their survival and ensuring an enduring, sustainable future. The key is 4IR technologies, particularly AI-powered and ML-powered innovation.
AI tools can process and interpret huge volumes of data collected from the production floor to detect patterns, study and predict consumer behavior. Also, to detect irregularities in the production process in real-time and much more. These tools help manufacturers in gaining an understanding of the entire manufacturing process in factories across all regions. Because machine learning algorithms are used, AI-powered systems can learn, adapt and continuously improve.
This is essential for manufacturing companies to prosper due to pandemic-induced rapid digitization.
According to McKinsey, firms that have embraced AI have experienced cost savings and growth in revenue. For example, 16% of the companies surveyed saw a 10-19% decrease in their costs, while 18% experienced a 6--10 percent increase in revenue overall.
AI systems also allow predictive analytics, which can help solve operational problems and disruptions in the supply chain and the workforce. For example, a McKinsey report indicates that AI can boost the accuracy of forecasting in the manufacturing industry by 10-20%. This can translate to a 5% decrease in inventory cost and an increase of 2-3% in revenue.
Other advantages associated with AI in manufacturing are:
-
Predictive maintenance can decrease unexpected downtime.
-
Establish near-shore manufacturing facilities with the latest manufacturing technology (3D printers and robots) to cut the cost of labor and remain flexible despite disruptions in the supply chain
-
Design the most efficient, AI-powered design that maximizes effectiveness and reduces the amount of waste
How Will AI Change Manufacturing?
The rise of 4IR technologies will bring in the age of digital manufacturing and smart factories. According to IFR (International Federation for Robotics), it was estimated that there would be 2.7 million robots in industrial use in operation in factories around the world in the year 2020. This is a 12% rise compared to the year before. Moreover, with digitization projects expanding exponentially, this trend is predicted to expand even more.
Manufacturing companies will keep investing in new technologies such as AI and machine learning to lower manufacturing costs and speed up the speed to market. In addition, after the global pandemic, businesses are working to make their operations more resilient by implementing technology that can automate the process and forecasting disruptions. They also help to control all processes.
-
Manufacturers are more often introducing AI robots on the production line to create a safer environment and boost productivity.
-
With the help of AI manufacturing, companies can identify problems with their products and other issues related to quality or design.
-
By combining AI, ML, and industrial revolution technologies, designers can develop thousands of design concepts in just a few minutes. These design options assist manufacturers in creating end products with unique designs.
Key Benefits of Artificial Intelligence in Manufacturing
Simply said, artificial intelligence solutions can help manufacturers of all sorts operate more efficiently and with greater efficiency. However, before diving into specific application scenarios, it's worth looking at the three main benefits of using AI for manufacturing.
Drive Revenue
Manufacturers can use AI to boost revenues in many ways. From forecasting and anticipating demand to designing intelligent connected products that can create novel and creative business models.
Cut Costs
Apart from generating sales, AI can also help to cut costs dramatically. For example, manufacturers can use AI to anticipate maintenance needs before they occur, enhance manufacturing and supply chain efficiency, and study service patterns to improve product design and cut down on the cost of the warranty.
Avoid Risks
Risk reduction is another benefit not to be ignored because the consequences are important. Manufacturers can use AI to spot product defects in the early stages. It helps improve quality procedures to lessen the risk of producing a product and resolve customer service issues before they cause a large impact. It can also even reduce dangers to health by predicting the potential for harm from specific processes.
Direct Automation
IIoT is a network that connects every IoT-connected gadget to factory floors, linking manufacturing processes and big data and making them programmable through the logic controller. Greater use of precision sensor equipment means that data can be recorded, generated, and analyzed in all areas of the manufacturing process, including temperature to the selection of items and packing.
Programmable logic controllers equipped with AI capability to learn deep-learning can respond automatically to the automatically generated data and even make adjustments to the most minute of tasks without human intervention. The analytics derived from big data processed by AI can significantly improve efficiency throughout production and can be controlled remotely.
24/7 Production
Human beings are living creatures and require regular maintenance, e.g., sleep and food. For any production facility to remain operational 24/7, it is imperative to establish shifts that employ three humans every 24 hours. Robots never get hungry or tired. They can work on the production line 24 hours a day.
This permits the development of manufacturing capability, which will be becoming required to meet the needs of global customers. In addition, robots are efficient in several areas, like the assembly line and packing and packing departments. As a result, they can drastically reduce turn-around times in various areas of business operations.
Lower Operational Costs
Many companies are looking at AI's introduction into AI in the manufacturing industry with fear since it is a massive capital investment. However, the ROI is substantial and will increase with time. When intelligent machines start to replace the day-to-day tasks of a factory floor, companies will see lower operating expenses and the use of predictive maintenance to minimize downtime for machines.
Customers are becoming more demanding of custom-made, unique, or personalized items. Still, they also are looking for the best quality for the money. With the advancements in technology, such as 3D printing and IIoT connectivity to devices, it's becoming more affordable and easier to meet the demands of consumers. Using virtual and augmented techniques for design ensures that the entire manufacturing process is more efficient, efficient, and cost-effective. Combining machine learning with CAD will mean that machines can be developed and tested using the form of a virtual model before they go into production. This reduces the costs of trial and error machine testing.
Predicts Equipment Failure
It is also a significant AI application in the manufacturing industry. The most frequent usage of AI and ML for manufacturing purposes is the need to enhance the efficiency of machines. Manufacturers are faced with the challenge of sudden failures of machinery. It may appear perfect on the outside. However, it performs poorly when we use it. It reduces productivity.
This is the second major reason for the increasing need for AI in the manufacturing industry. AI software development companies are creating top-of-the-line robotic solutions and automated maintenance tools by using the power offered by AI, ML, and predictive analytics technology. These tools warn of early equipment damage and help stop machinery from shutting down accidentally.
Use Cases of Artificial Intelligence In the Manufacturing Industry in 2022
We now understand the main advantages of AI for companies. So let's look at some of the more powerful uses cases more deeply.
Product Quality Assurance
It's not uncommon to see people performing visual inspections to spot defects in the production line. Unfortunately, human perceptions, attention spans, and energy levels aren't as robust and can lead to costly mistakes. AI can help people make better use of their energy elsewhere, and AI lets them achieve this.
Manufacturers can use AI using human-in-the-loop inspections to enhance quality assurance and significantly reduce the chance of manufacturing defects and flaws. Additionally, this method frees workers' time to focus on more strategic work.
Smart cameras, as well as other AI-powered technology, can look at images and detect abnormalities. These image recognition programs analyze the product's features, such as curves, color, corners, and curvatures. Then assess the product against a set of standards to determine if they meet or fail the inspection process.
Although the method varies depending on the item, Image recognition software is extremely adaptable. It can be used on nearly any item with high precision. A McKinsey study revealed that image recognition programs could improve the detection rate of defects by as much as 90% compared to human inspection.
Robotics
Industrial robots, sometimes called manufacturing robots, can automate repetitive tasks and reduce or limit mistakes made by humans to a minimal amount. The applications of robots in factories differ. They can be used for welding, assembly painting, product inspection, picking and placing die casting, drilling, grinding, and glass making.
Industrial robot has been used in manufacturing facilities since the 1970s. However, with the advent of AI, industrial robots can monitor their performance and accuracy and train themselves to improve. In addition, certain manufacturing robots come with machine vision which helps the robot in achieving exact mobility in difficult and chaotic conditions.
Health & Safety Risk Avoidance
Creating a safe workplace is essential for various reasons, including protecting employees and improving morale. This is particularly important to the chemical industry, which is strictly controlled by a combination of international and national operating procedure guidelines and health safety, environmental, and safety elements.
Traditional preventive strategies such as annually scheduled training, posters, and protective equipment leave much opportunity for unsafe work and risks. AI is a better option.
By using industrial IoT information, companies can track worker activities, machinery compliance, and the causes behind safety shutdowns in real-time. In addition, employees can wear smart devices that track the body's temperature and other biometrics that alert the supervisors of health issues.
Machine learning could help develop surveillance systems using video to determine the presence of workers who aren't wearing the appropriate safety equipment or performing unsafe activities. With sensors located on the shop floor, machine learning can also provide insights into the effectiveness of safety systems. This allows them to pinpoint the causes behind shutdowns and identify key signs of problems with the machine so facilities managers can address them before accidents occur.
Helps in Predictive Maintenance
One malfunction in the equipment can cause significant disruption to the production process, leading to an increase in the time of downtime and cost. So, timely and proper maintenance of the machine is essential. Unfortunately, this is frequently neglected until a major failure occurs.
To meet these challenges, Manufacturing facilities are currently deploying machines powered by ML to make predictions, in addition to AI solutions determining when equipment requires regular maintenance. Furthermore, in certain situations, IoT and cloud sensors are integrated into the equipment, that help predicts the timing of maintenance. This helps in overcoming the most serious issues with equipment that could be a problem soon.
Implementing AI-powered manufacturing tools will help automatize manufacturing processes, allowing manufacturers to develop smart operations that can cut costs and downtime.
Inventory Management
Inefficiency in managing inventory can lead to significant costs for manufacturing companies. By using AI tools, manufacturers can keep track of their orders and add/delete inventories. Machine Learning plays an integral part in managing inventories with demands and supplies.
Artificial Intelligence is powering manufacturing processes in new ways. Use AI to change your business processes, improve the quality of your product, and lower costs.
Quality Checks
Some flaws aren't large enough to be detected by the naked eye, even if an inspector is extremely skilled. But machines can be equipped with cameras that are many times larger than the eyes of our own, and because of that, they can detect even the most minor flaws. Machine vision lets machines "see" the products on the production line and detect defects.
Generative Design
Generative design is the process that requires a program to generate various outputs that satisfy certain criteria. Developers or designers enter design objectives and parameters, such as materials, manufacturing techniques, and costs, into generative design software to investigate design options. The software uses machine learning methods to discover every time what works and what does not.
Key Takeaways - Why Manufacturers Must Adopt AI Sooner
A McKinsey study found that firms taking on digital transformation in manufacturing are at the forefront of the field. They are embracing 4IR technologies, including Big Data Analytics, AI AR, VR, and IoT, as well as predictive analytics automation, robotics, and automation as well as others.
In the end, they realized various advantages in terms of efficiency and productivity as well as costs. They include:
-
30-50% reduction in the machine's downtime
-
15-30% increase in work productivity
-
10%-30% increase in throughput
-
10-20% reduction in quality-related costs
Early adopters are already winning competitive advantages by significantly reducing operating expenses, speeding up speed-to-market, and improving efficiency. The benefits will only increase with time and widen the gap between early adopters and the slow adopters within the field.