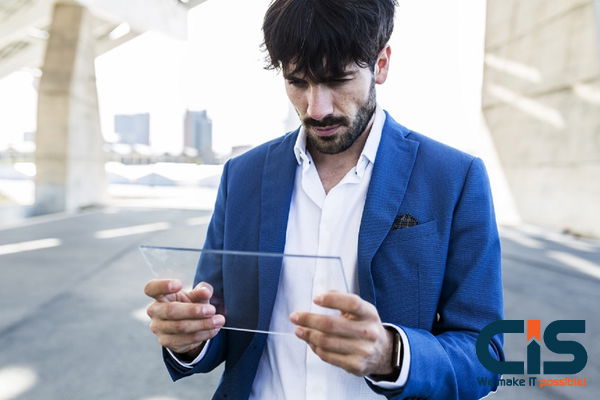
Organizations looking to deploy Industrial IoT (IIoT) must address both design and implementation challenges associated with industrial IoT architecture to succeed with deployment. IIoT technology connects sensors and devices to industrial control systems and energy networks in order to increase productivity and processes while strengthening processes overall. IIoT integrates advanced computing infrastructures such as data storage infrastructures, machine learning platforms, analytics engines and strong communication platforms in order to be truly useful tools.
The design of IIoT architecture can be complex. Communication network and control layer issues must also be considered carefully for best results. Innovation of IIoT-related technologies in the industry combined with investments that ensure it remains resilient against change will make the IIoT more adaptable in the long term and bring even further benefits; machine learning tools may prove particularly effective for operations analytics and performance optimization purposes.
What Is The IIoT?

Industrial Internet of Things is an umbrella term encompassing tools and apps used by large organizations to establish an interconnected environment from core to edge of their organization. Additionally, physical infrastructure like shipping containers or logistics trucks may also be part of Industrial IoT implementation, providing data collection points which help to react quickly to events and make smarter decisions more easily.
This technology builds off the Internet of Things (IoT), with many consumer applications like remotely turning off lights using devices like Amazon Echo that use Alexa voice recognition technology.
IIoT technology has quickly become an invaluable asset to industrial operations. As a commercial tool that can be applied in complex environments with complex infrastructures and heavy equipment, IIoT allows remote control of all factory HVAC systems - just one application which improves enterprise operations while simplifying operations overall.
How Does IIoT Work?
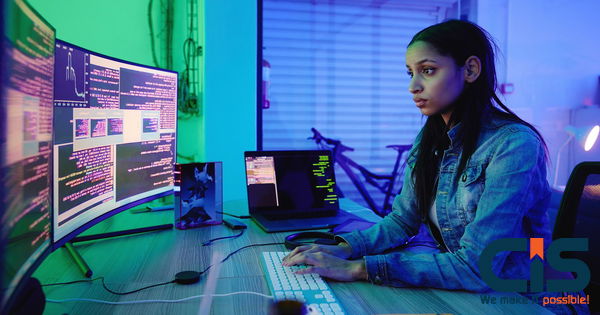
Companies are reinventing how they connect, monitor and analyze industrial data in order to reduce costs and drive growth. They do so by reinventing how they access it and taking appropriate actions based on it - all to reduce costs while spurring growth and making more informed business decisions. General Electric was one of the five founding members of the Industry IoT Consortium and can be credited for coining the phrase 'industrial internet."
IIoT (Industrial Internet of Things) is an initiative which utilizes data generated by industrial facilities for long-term benefit. Smart machines on assembly lines not only collect and analyze more quickly, but they can also relay vital business decision information more rapidly and precisely than before. IIoT (Internet of Things) is propelled by the convergence of IT (information technology) and OT (operational technology). The IIoT is a matrix network connecting devices and equipment together, collecting sensor-generated data before processing into platforms for integration directly onto platforms, creating new industrial applications with many economic opportunities and Smart Connected Products.
IIoT collects vast amounts of factory floor data via nodes and transmits it to servers for analysis before turning it into actionable insights via cloud platforms for businesses to make smarter business decisions based on target audiences and markets. As stated, IIoT acts as an edge device that directly connects actuators and sensors with cloud servers for transformation into actionable insights for better business decision-making.
What Is The Relationship Between Industry 4.0, IIoT And IoT?
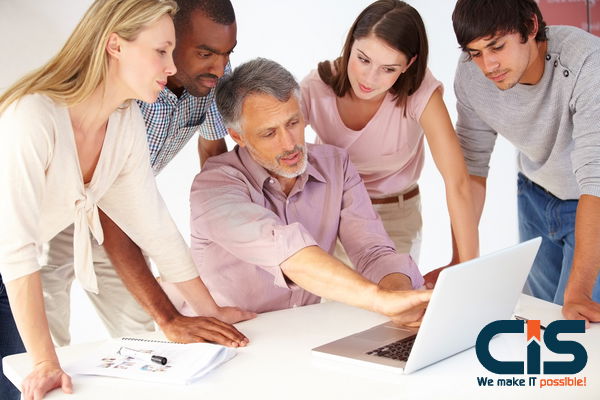
Industry 4.0 is part of the fourth Industrial Revolution, which refers to integrating traditional, automated manufacturing processes with intelligent technologies and autonomously communicating devices for efficient production processes. Industry 4.0 (also referred to as I4.0 or I4) was popularly coined in 2011 by Germany's government, which has advocated digitizing industrial processes extensively for two decades .
Companies say IIoT, as well as additive manufacturing, 3D printing and augmented reality, is one of the key pillars of Industry 4.0. Other elements, such as big data analytics and cloud computing, cybersecurity and horizontal/vertical integration systems, and simulations, can all play an essential part in its implementation. Autonomous machines communicate digitally within their environment, making human intervention less necessary, resulting in automating resolutions to issues previously only possible through human means.
Industry 4.0 encompasses IIoT, digitalisation, and corporate sustainability in general. IIoT drives Industry 4.0's existence; without it, there would not be Industry 4.0 today! IIoT itself, however, only encompasses data detection/transfer/computing/processing and domain-specific intelligent applications and apps.
IIoT Architecture
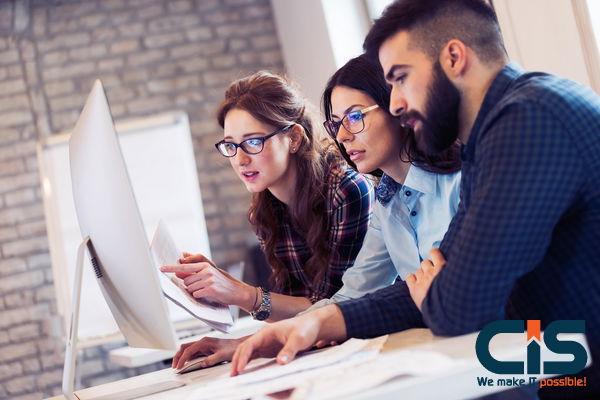
An industrial IoT (IIoT) architectural arrangement describes how digital systems are set up to facilitate communication among sensors, IoT devices, data storage facilities and other layers in a networked IoT device ecosystem. An ideal IIoT architecture should incorporate these key features:
#1. IoT Devices On The Edge Of The Network
An edge IoT ecosystem consists of connected objects close to their data sources - usually wireless actuators and sensors in industrial settings - plus a small computing device and endpoints for observation. Edge IoT equipment ranges from old legacy equipment such as cameras or microphones through cameras, sensors, microphones or meters, making up this network ecosystem.
What takes place at the edge of the network? Sensors collect information from their surrounding environment and any objects under surveillance before translating this data into metrics and numbers that an IoT platform analyzes into actionable insights. Meanwhile, actuators control processes within an observed environment or change physical conditions in which data production occurs - this process produces tangible actionable intelligence as actionable insights become actionable insights.
#2. Edge Data Management, Initial Processing And Edge Data Management
Intelligent applications relying on complex analytics require high-quality information as input; data can even be processed immediately at sensor levels if information needs are pressing. Edge computing offers the fastest route to answers as data is processed at its source - sensors. Analyses can then be performed on collected digital information or aggregated knowledge from digital streams rather than sending the entirety to data centers or clouds for storage. Once insights are gained through edge computing, processing can move on with further steps or analysis more rapidly without sending all your digital information back out again, as additional processing reduces data volume sent towards these centers or clouds.
#3. Cloud-Based Advanced Processing
Edge devices do have limited preprocessing capacities. While you should try to locate as close to the edge as possible to minimize native computing power use, users will require cloud computing services to perform more thorough and detailed processing tasks.
Cloud computing brings advanced insight and agility, offering powerful processing capability and the possibility to combine data from various sources for insights that wouldn't otherwise be available at the edge.
The cloud has the following characteristics in the context of IIoT architecture:
- This hub provides a secure connection to the system on-site, telemetry, and control of devices. The hub can provide remote connectivity between on-premises and other systems across multiple locations if required. It manages all communication elements, including connection management, secure communication channels, device verification, and authorization.
- Storage is useful for storing information both before and after processing.
- Analytics is a tool that helps in data analysis and processing.
- An interface provides visuals for communicating the analysis findings to end users, usually via a web-browser interface, and alerts are sent via email, SMS, or phone call.
#4. Internet Gateways
Sensor data collected and converted to digital channels at the gateway for processing at this node of a data collection system's edge are transmitted over the internet for further analysis by further gateways before being uploaded into the cloud for storage and analysis. Gateways remain part of edge systems' data collection systems near sensors/actuators as part of a data collection systems' edge, performing preliminary data processing before going further downstream for uploading into cloud services.
Gateways can be deployed in hardware or software form:
- Hardware gateways are devices that can be operated independently. Wire-based (analogue or digital) and wireless interfaces provide the downstream sensor connection. These devices offer Internet connectivity directly or through a standard router link.
- Software PCs can be equipped with software gateways instead of hardware gateways. Software gateways can be installed in the foreground or background, providing upstream and downstream communications links, while the PC provides physical interfaces. Software-based gateways can access visual settings for sensors and data display via user interfaces.
#5. Connectivity Protocols
Data transfers across IIoT require protocols. They should be well-defined and secure while also adhering to industry standards ideally. Protocol specifications could include their physical properties and cable configuration, method for setting up communication channels and format of transmitted data over those channels, among others.
The following are some of the most common protocols that are used in IIoT architecture:
- Advanced Message Queueing Protocol AMQP: It is a compact data-encoding, connection-driven, bidirectional message transport protocol. AMQP was designed for IIoT cloud connectivity, not HTTP.
- MQ Telemetry (MQTT): It is a compact message transport protocol. MQTT benefits IIoT devices due to its small message frame size and minimal code area.
- Constrained Application Protocol (CoAP): It is a datagram-led protocol which can be deployed through a transport layer. This includes the user datagram protocol. CoAP is an abridged version of HTTP designed for IIoT.
#6. IoT Platforms
IIoT platforms enable organizations to orchestrate, monitor, and control operations across a value chain. Platforms monitor device data while managing analytics, visualizations, and AI duties from edge devices to sensors - sometimes all the way up to cloud storage services!
IIRA can be a handy reference point when developing complex IIoT systems, offering iterations and feedback during design processes to optimize system outputs. According to its frameworks, businesses should follow an iterative design method featuring iterations. Furthermore, reports state that IIoT designs could be tailored specifically for businesses in industries like energy or healthcare - or customized specifically for government use!
Read More:
What are the 9 Examples of Internet of Things or IoT?
The Benefits Of IIoT
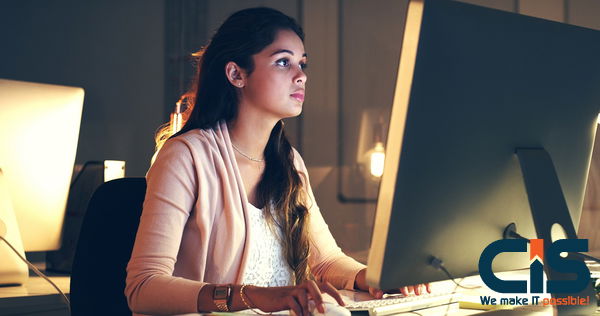
Industrial IoT boasts several key benefits. Here are their highlights.
#1. Boosts Efficiency
IIoT's primary benefit lies in helping businesses automate and increase operational efficiencies. Sensors that monitor physical equipment's performance can also be linked to software solutions to provide insight into individual equipment or fleet efficiency, data-driven decision-making, and remote production monitoring processes.
#2. Production Increases
Organizations using IoT-enabled manufacturing processes can expect their equipment use to increase with IoT data flows. Access to constant streams of operational information gleaned from connected devices provides invaluable insight into optimizing machine performance and increasing effectiveness, all while freeing up employees for more strategic production-related roles. Using IIoT devices also improves human capital utilization as smart devices can be utilized for menial, repetitive or hazardous tasks allowing employees to focus more strategically.
#3. Reduces Errors
Its Organizations using IIoT must automate production to increase customer satisfaction and brand recognition while decreasing error-causing inefficiencies caused by human workers in industrial operations. By cutting back the human factor from industrial processes, inefficiencies that lead to defective products off the assembly line are eliminated, leading to greater profits with higher customer loyalty and brand awareness for your organization.
#4. Predicts Maintenance Requirements
Predictive Maintenance (PM) is an approach designed to prevent asset failure through data analysis that reveals patterns in production data to recognize patterns and anticipate impending problems. Industrial Internet of Things (IIoT) sensors installed into industrial equipment allow notifications for condition-based monitoring to be sent out automatically, including temperature, humidity and ambient variables like materials composition that impact transportation factors; data can then be used for predictive maintenance to avoid failures while cutting expenses and shortening downtime.
#5. Worker Safety Is Paramount
Employee safety is of utmost importance Smart Manufacturing offers increased workplace and employee security thanks to IIoT sensors working together with integrated safety systems to monitor employee and workplace security. If an accident happens, senior management could step in quickly with solutions - for instance, informing all facility activities of its occurrence while stopping all related activities, reporting it and notifying all necessary parties immediately or providing useful data to prevent similar incidents.
#6. Saves Energy Costs
The industrial sector accounts for much of the world's total electricity use, which poses serious environmental and profitability threats. With IoT devices becoming more energy-efficient each year, they could help mitigate industrial sector energy use while saving maintenance costs at once. Sensors and gadgets could help monitor your system constantly to detect inefficiency that results in waste - for instance, regulating temperature, water usage, humidity levels or lighting across your facility - not to mention saving you money! Sensor technology continues to develop more energy efficiently over time, so it will only benefit your bottom line!
#7. Customer Experience And Field Service Are Improved
Customer experience and field service delivery are enhanced. IIoT provides an effective means for improving field service delivery. Time, context and participation by technical personnel all play key roles when considering its usefulness in any operation. Real-time visibility allows OEMs, end users and all interested parties to stay abreast of issues as soon as they arise - thus giving real-time visibility over data that allows for timely notification if problems or risks appear.
What Security Concerns And Challenges Arise When Adopting IIoT?
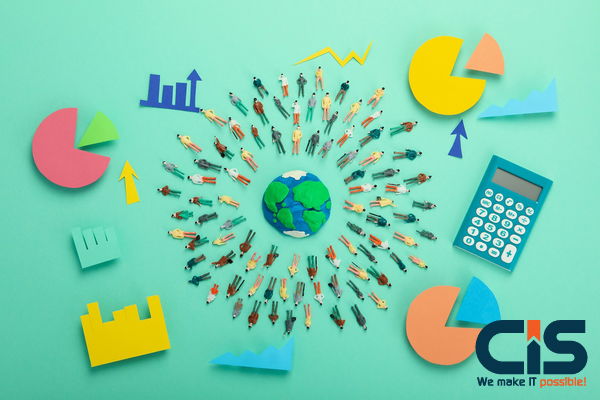
IIoT promises to revolutionize how industries work, yet to ensure its full impact is realized, and strategies must support digital transformation while upholding security. Companies and industries that employ operational technology should have an in-depth knowledge of worker safety and product quality issues. With increasing internet integration comes many new challenges for these enterprises to face. Implementation of IIoT should take three areas into account, which include security, scalability and availability. While industrial operations may already have experience dealing with issues of availability and scalability due to being established for some time now, other businesses might experience challenges integrating this new technology due to legacy systems or processes still used today that make adopting new tech more complex than desired.
Smart devices have raised concerns regarding security and accountability. IIoT users bear primary responsibility for keeping their devices and setup secure; however, manufacturers of connected devices also bear an obligation to their users when releasing products onto the market. They should offer preventative measures or solutions when security problems occur. Cybersecurity has never been more crucial as increasingly serious security incidents occur. Hackers who gain entry to connected systems may pose major threats, potentially leading to the shutdown of business operations. To safeguard the physical and digital components of IIoT projects, enterprises and industries adopting it must plan and operate similarly to technology companies.
Adopters of IT in industrial operations face the additional difficulty of combining it with industrial operations in an environment where data must be protected, in line with European Union privacy general data protection legislation (GDPR), for example. Processing user data should abide by such legislation as GDPR; collecting log data must respect privacy regulations such as GDPR, while personal information such as personally identifiable data (PII) should be separated and kept encrypted within an encrypted database to avoid risks of sharing it publicly on cloud storage services such as G Suite and similar solutions. Concerns have been voiced regarding fragmented technology within IoT, including IIoT systems. Interoperability between IIoT devices may be compromised due to differences in usage, such as using different standards/protocols such as MQTT/CoAP etc.
What Is IIoT Architecture, And Where Should Organisations Start?
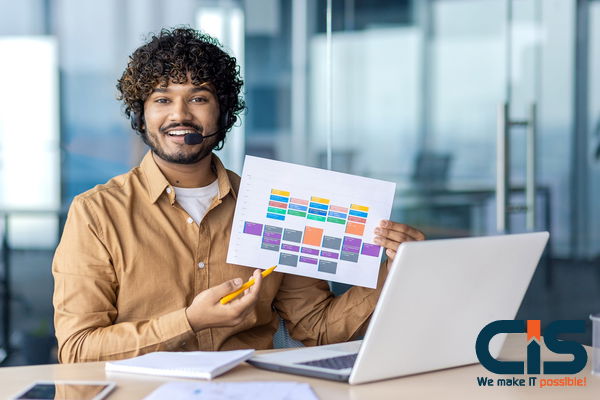
An IIoT architecture can be defined in three layers. These layers include device, communication and semantics. Device architects define how devices will interconnect through communication systems on different layers; communications protocols exchange useful data, while semantics provide context around this structure that reinforces business goals.
To accelerate development, architects should begin designing IIoT deployments by creating an ontology - the relationships among different layers - and investing in four categories of industrial IoT technologies. IIoT architecture includes layers for device interaction, communication and semantic interpretation.
Communications And Security
Achieving optimal functionality within an industrial IoT architecture relies heavily on investments made into communications between plants, facilities and Smart Supply Chains. Sensors, data exchange, and environmental monitoring capabilities provided by IoT enable organizations to address concerns related to management, safety, flow state analysis of machines/materials, and general operations. 5G and 10 Gbps broadband wireless connectivity will add new capabilities to IIoT. Virtual networks, for instance, could host computing and analytic workloads securely within cloud infrastructures. Application users requiring remote monitoring, analytics and decision support at multiple industrial sites will find this beneficial. Connectivity for local control connectivity will be established over optical, wired and wireless networks with similar levels of security as cloud systems.
Open Data Platforms And Industrial Device Networks
Open systems serve to guide the creation of a shared information model. At the same time, industrial device networks generally utilize transport and communication protocols with which all nodes comply to facilitate easier management. Data governance automation in facilities should restrict sharing/device access depending on need; when designing IIoT platforms, architects should keep privacy requirements and strong protection mechanisms top of mind for strong protection measures of data and communication paths in mind.
Auberdem
Intelligent algorithms are capable of performing many operations-related tasks efficiently. This includes classification, prediction, and optimization tasks. AI models may support real-time decision-making, learning and data analysis, while others address optimization problems directly. Organizations should plan as much as possible when adopting process optimization into industrial systems, as the implementation is time-consuming and costly.
System Control
System Control mes In a smart factory or facility setting, interacting systems require an understanding of all existing independent systems that make up its architecture. An architectural designer needs a detailed knowledge of services offered, information exchanged, and any scheduling conflicts that might prevent exchange. The key component to creating successful designs lies in controlling system interactions such as the abstraction of services provided, information transferences between exchanges, and timing between exchanges.
IoT Examples
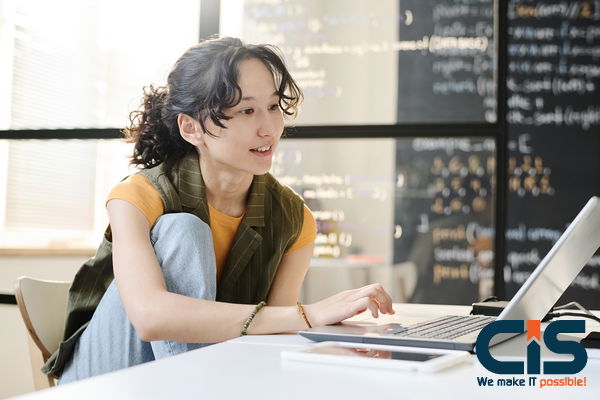
IIoT technology has found widespread applications within many notable companies and industries, from manufacturing to retail - producing tangible business benefits for these users. Here are a few IoT examples which have resulted in positive business outcomes:
#1. PepsiCo Implements Iiot To Track Assets
Implementing IIoT components within shipping, fleets, and packaging enables PepsiCo to use embedded IIoT sensors embedded within shipping fleets or packaging to keep inventory levels balanced between supply and demand. Their wide variety of technologies allows PepsiCo to adapt products according to changing market conditions while managing inventory systems' visibility and automating replenishment policies based on IIoT technologies embedded into inventory levels for inventory level tracking purposes.
#2. BMW Creates Digital Twins For Its Products Using IIoT
Industrial IoT apps such as digital twins use sensors to accurately simulate physical characteristics and details about products down to every detail, creating an accurate simulation. At BMW, immersive technologies, AI, and IIoT combine to form digital replicas of factory production processes. These enable development, evaluation, and optimization without incurring costs, operational cost or risks to optimize products in realistic settings without incurring extra expenses or risks.
#3. L&T Uses IIoT To Reduce Costs And Monitor Remote Locations
Energy and utility sectors utilize large operational infrastructures which may not be suitable for human operators due to hazardous environments; when this is the case, IIoT devices can gather vital operational data without human operators' presence - something Larsen & Toubro is taking advantage of by installing its Green Hydrogen Station that can be remotely monitored in Gujarat, India - using this advanced monitoring technique reduce operating and energy costs as well as gain valuable insight into its operation through using IIoT!
#4. Irish Distillery Uses IIoT To Monitor Environmental Conditions
Food and beverage manufacturers and retailers depend heavily on being able to produce their goods under ideal environmental conditions, with Industrial IoT helping monitor any changes that could alert floor managers of product degradation before it occurs. Industrial IoT technology can even be deployed at distilleries that produce alcoholic beverages which operate in delicate environments - the perfect example being Frilli Distillation Plant in Ireland, which recently implemented IIoT technology with one beverage brand to automate, enhance efficiency, and create uniform processes across operations.
#5. Airbus Builds A Smart Factory Using Bosch's IIoT Platform
Airbus' goal with their smart factory built using Bosch's IIoT Platform is to eliminate errors by embedding IoT sensors in machines and equipment on its production floor and equipping employees with wearable technology like smart glasses for industrial purposes - one mistake in manufacturing processes could cost millions, so Airbus and Bosch's "Factory of the Future" is employing digital intelligence for optimization of operations and productivity optimization.
Build Your IIoT Architecture With These Tools
Complex IIoT system development is guided by the Industrial Internet Reference Architecture. Established frameworks suggest organizations utilize system-based approaches when planning architectures for IT and operational technology applications like transportation, energy or healthcare services. It includes specific reference architectures within an industry segment like transport or energy that serve as guides when developing such complex systems.
Early IIoT plans must include an implementation perspective to understand usage patterns between components within an IIoT system. An implementation viewpoint includes lifecycle and utilization of technology infrastructure communications sensors machine-learning for functional component implementation of systems. Organizations might consider adopting a three-tier architecture pattern consisting of edge platform enterprise service layers aligned to systems currently in use as examples of such utilization patterns; alternatively, IIRA can help IoT project managers outline an organizational approach and look at goals and systems from a framework-driven viewpoint.
Architecture firms should design an IIoT architecture tailored to the requirements of their organization:
- What is the goal and vision of the architecture? Who are the stakeholders involved? What do you want to achieve? What will machine learning do or inform better over time? What are the possibilities for improving decision support? What determines the success of a system? A planning strategy based on outputs is essential.
- For architects and IoT leaders to be guided in their approach, have them read and evaluate IIRA. During the design stage, technical stakeholders must align the business perspective with the functional perspective to define the communication layer, the interfaces, the data, and the interactions of the systems with the surrounding environment.
- Define your project's scope, considering future implementations and viewpoints. Define functionality, including the business, information, operation, control, and application domains and decide on the most appropriate deployment pattern.
- Identify the fundamental capabilities of architecture in terms of tasks and roles within each functional domain. This will help coordinate functionality throughout the system.
- Define KPIs, feedback and success criteria. Define the program relationships to include all stakeholders' views and opinions.
- Assure the organization is prepared to plan, implement, measure, and correct as part of a continuous, iterative improvement cycle.
Takeaway
Industrial IoT (IIoT) has quickly become an essential service provided by cloud providers like Microsoft and Amazon Web Services. IIoT extends advanced data analytics capabilities and cloud computing to industrial applications like factory operations, equipment maintenance, personnel safety management and supply chain management - not to mention simulating and testing products within digital environments for simultaneous integration between physical systems.