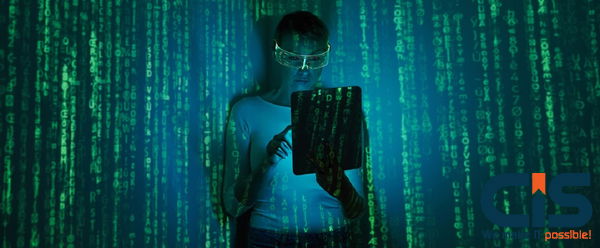
Manufacturing is undergoing an era of the digital revolution. Advanced technological advancements, advanced data analysis, and connected devices enable companies to increase efficiency, productivity, and accuracy drastically. Digitalization is changing how products are created, manufactured, and used and is also changing the process, operations, and energy consumption of factories and supply chains.
One of the significant factors driving digitalization is the capacity for companies to increase their agility and responsiveness in response to changes in market conditions and consumer requirements. Manufacturers can match their production schedules to demand throughout the year, avoiding waste and unhappy customers.
Additionally, removing manual processes and implementing automated tools such as robotic process automation can help improve processes and enhance performance monitoring and decision-making, avoiding rework, downtime, errors, and bottlenecks. This, in turn, will cut time and expenses.
What is the Manufacturing Industry?
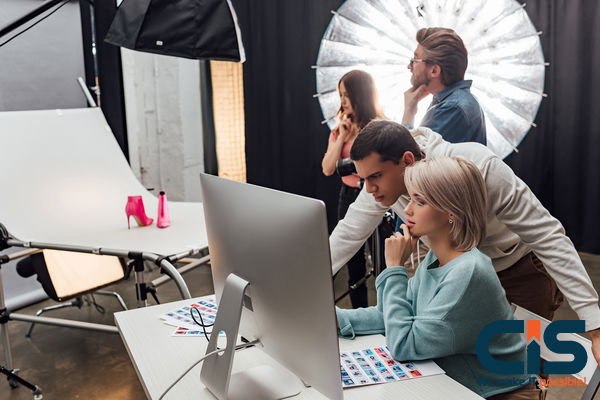
The manufacturing industry converts raw materials or components into final products offered for sale on the marketplace. These can be finished goods readily available in retail stores or components utilized during the manufacturing process.
Before the advent of industrialization, most of these items were created by hand. In the years since, automated machines have been created to produce mass quantities of these items, allowing industries to accomplish their processes faster with more precision. Because they require less work, this process lowered costs and made the product less expensive.
Many industries depend on manufacturing for their operation for their operations, including:
-
Food and beverages
-
Textiles
-
Paper and wood
-
Machinery and metal
-
Electronics
-
Furniture
-
Transportation and more
Manufacturing is essential for the economy since it employs an enormous portion of the workforce and produces the materials required by various industries worldwide.
Why is Digital Transformation in Manufacturing Important Now?
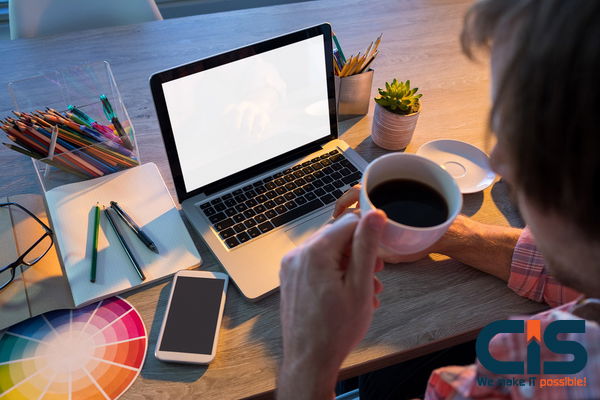
Expectations of customers and increased competition are the primary factors driving the digital revolution in manufacturing, as in other industries. Utilizing digital technologies manufacturing companies can increase efficiency and speed, boost production, lower costs, and offer more satisfying customer experiences.
COVID-19 has also proven how important it is to embrace the use of digital technology in manufacturing. In the course of the epidemic, manufacturers confronted operational issues that highlighted the weaknesses of their existing business. For example, having real-time information on the supply chain can allow manufacturers to respond more quickly to supply shortfalls and surges in demand during the pandemic. Below is an image from IBM and The Manufacturer's study that shows companies' strategies during the outbreak and how everyone could benefit from digital technology.
Digital Transformation Trends in Manufacturing
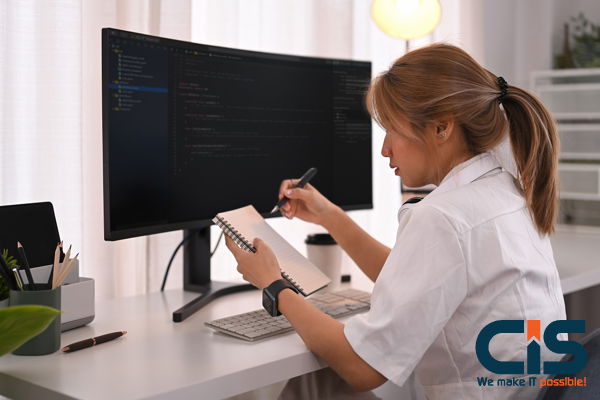
It's an exciting time for the manufacturing industry since Industry 4.0 is being developed. Many firms are shifting gears using the help of modern technology to automatize the manual process.
The year 2022 will continue to follow the trends of digital transformation that have been set over the past few years. The difference is not as much like technology used but more in the increasing number of companies that are moving to digital.
Let's review the top trends in digital transformation to be on the lookout for in 2022.
IIoT

The Internet of Things or IoT is the internet of various physical objects embedded with software. It's a web of interconnected sensors and electronic devices that collect and exchange information.
We're all familiar with these products in our homes, in the form of Digital voice-based assistants, such as Alexa or smart TVs lighting bulbs, thermostats, or?
In the same way, similar to the IIoT, also known as the Industrial Internet of Things, has the machines on the manufacturing floor connected via the internet. The system collects information to enable AI and to perform predictive analysis.
IIoT is changing the manufacturing industry completely. It's transforming how products are manufactured and distributed.
A survey conducted in 2019 found that 63% of the manufacturers believe that the introduction of IoT solutions will boost profits in the next five years.
Compared to 2015 in 2015, IoT spending worldwide in discrete manufacturing was around 10.4 billion U.S. dollars. In 2022 it has increased by four times to reach forty billion U.S. dollars.
B2B eCommerce
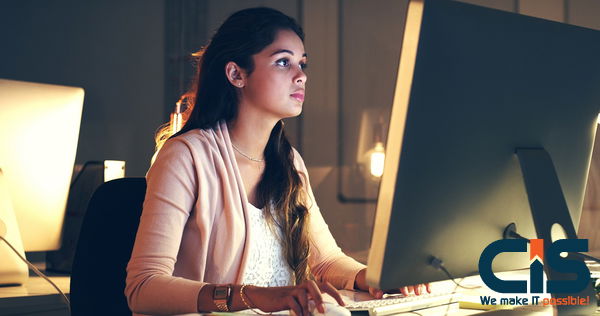
Today's B2B eCommerce platforms have to respond to the needs of B2B buyers rapidly, and these tend to be similar to the needs of B2C customers. Maintaining the B2C experience is a challenge since B2B customers require customized checkout processes, price policies, and personalization of product data, and other complicated functions are running within the background. However, companies like Saltworks and Samuel Hubbard are great examples of manufacturing cases involving digital transformation studies that managed to transform their stores digitally through the implementation of OroCommerce. This allowed the use of one site for segmentation and multichannel capabilities. It also improved their models of business.
3D Printing Technology
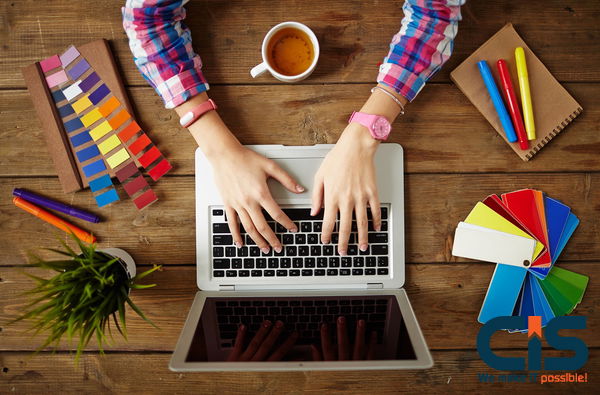
3D Printing is a much-discussed digital transformation technology that is used in manufacturing. This technology helps businesses create quicker and more affordable prototypes. Innovations in this field have reduced costs by half while providing double the performance.
It's a cost-effective method for product designers to find a solution and test their products. It also aids industrial manufacturers in creating highly sought-after products.
The automotive and aerospace manufacturing industries are already using this kind of technology.
Next Generation Manufacturing Employees
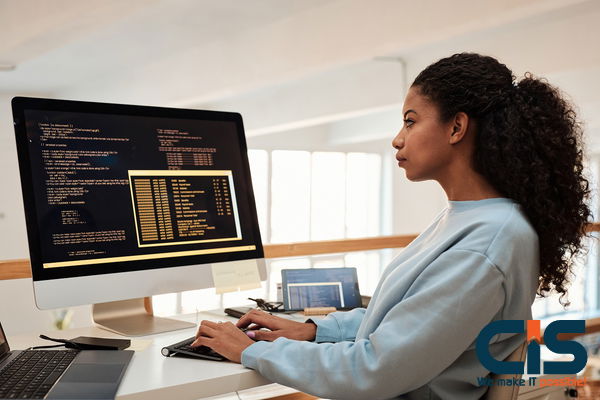
This is about people and their skills.
It's clear that as technology becomes the primary source of repetitive work, many conventional manufacturing positions will fade out. Additionally, due to increasing demand for supply chains, businesses are automatizing processes to increase production speed.
However, I am not saying that jobs will vanish out of the sector. Humans will be at the core of the manufacturing IT solutions sector. However, they require new capabilities. Some of the jobs that are in high demand are:
-
Data analysts
-
Software engineers
-
Programming for IoT robots, robotics, and automation
-
Customer service
-
R&D, product development
-
Marketing and sales
As the nature of their work shifts away from the traditional manufacturing process workers, they will have to acquire new abilities.
Machine Learning and AI
AI, also known as Artificial intelligence, is the development of intelligent hardware or software that can duplicate "human" behavior, such as solving problems and learning.
The most valuable benefit for any business moving to digital is its data. In light of the sheer volume of data gathered by machines, it is crucial to use algorithms for rapid actions. This isn't possible to do as efficiently swiftly, accurately, and quickly by humans.
' Data quantity and ' processing capability' have thus become two significant factors in adopting Artificial Intelligence-based technologies within your manufacturing. It's also why your manufacturing will be more efficient and less inefficient.
5G and Smart Manufacturing
Everybody was talking about 5G for the past few years. However, this year is crucial as 5G is finally entering the realm of manufacturing.
Industry 4.0, also known as Fourth Industrial Revolution, is bringing in a new era of smart factories that are connected devices that can communicate and make autonomous decisions. But, this change cannot be achieved without 5G.
This 5th-generation mobile network is speedier and more robust, capable of handling fully integrated IIoT in the intelligent factory. 5G's superior capacity, wireless versatility, and low-latency performance are the default option to help manufacturers.
Certain companies are already testing the technology. Audi, the car manufacturer, has already implemented 5G in support of its robotics. It has cut 30 percent to 50% of their time to deliver.
Predictive Maintenance Innovation
Manufacturing has relied on the application of technology. As per a study of ITIC in 2019, 86% of companies in the manufacturing industry say that a minute of downtime will cost as much as $300,000. In the era of "always-on" and remaining connected, the numbers are expected to increase shortly.
There was a time when companies would schedule regular maintenance for their equipment to check for any malfunctions that were not noticed. This would also lead to a stoppage in production and incur a cost.
With the increase in digital tech, machines are built with sensors that send messages to inform workers that maintenance is needed. A real-time alert system and response system and the ability to predict maintenance can detect mechanical problems before they occur.
Now! Isn't that cool?
Agility and Responsiveness
The most significant benefit is that technology is helping our companies focus on increasing the speed and responsiveness of their products in response to the changing needs of customers and market trends.
If we could reduce the amount of time we need to prepare, receive the order, plan, and then process an order from a customer, nothing else like it.
This will benefit manufacturing firms. They'll be able to keep pace with production cycles and rising demand for products. The better an organization can match these two fundamentals, the greater the agility they can bring to their processes.
Innovating Manufacturing Industry with Digital Transformation
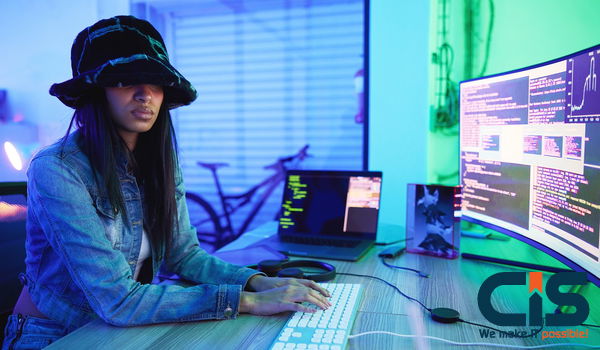
A key element of success for Digital Transformation is using data that is already in use and all the available information, and, most importantly, the collective knowledge of an open, agile new digital environment. Instead of just optimizing one production process, it is essential to be aware of the broader context and reap the real advantages of using the technology available.
Digital Advisors demonstrate how this can be done using an HPE Digital Journey Map. It is built on three fundamental capabilities of a modern organization that include digitization at the Edge and a cloud-enabled IT supply chain, and an infrastructure for data that can connect these three. The framework is comprised of 4 "Journeys," all of that is designed to achieve business goals that are contained within the structure of a digital plan:
Gain Insight and Control
The more sensors are placed in the vicinity, the better it's possible to record and analyze manufacturing automation processes and use patterns. Through the recorded data, production processes are more efficiently controlled, and product development could be better aligned with the customer's actual requirements. An example of this is electro-mobility battery manufacturing. It's a complicated process because chemical, mechanical, and electrical requirements must be combined and fulfilled. The size and the cumbersome chain generate much information to be saved, retrieved, and analyzed.
Modernize and Move
We will look at the development of an efficient supply chain. What technology should be employed? Should I use cloud-based capabilities? Where do I require the necessary expertise within the data center or in areas where data is generated at the edges? These are the issues to be addressed on this trip.
Look at an example for a successful implementation of a Hybrid-IT infrastructure with SAP S/4 HANA in a pay-per-use-Model, which meets two functions at the same time: an ERP environment based on the newest technology reflecting business processes and a high-performance engineering platform satisfying the research and development department of a high-tech company.
Redefine Experiences
Digitalization alters the user experience on edge, but it also alters the method that people work and the effectiveness and efficiency of employees. Today, we can increase work satisfaction by better man-machine collaboration or freeing up employees from repetitive tasks.
Video analytics tools like ones that use software like OpenVino toolkit (Open Visual Inference and Neural Network Optimization (Open Source/Intel (r)) provide automated and AI-based identification of flaws and anomalies in manufacturing processes, allowing workers of quality assurance. They are also able to protect workers.
Intelligent cameras can monitor the entry of a dangerous zone and detect any violations of the protection rules. If an employee attempts to enter a dangerous zone without the appropriate safety equipment, the system will block access.
Accelerate Development
The goal is to speed up product-to-market by improving collaboration between technology experts, engineers, and product managers. Sharing information among the various teams and understanding the impact on all data at every step of the process is an essential task.
An excellent example can be seen by looking at supply and production chains. Businesses may use various software or releases to manage their business, suppliers, or production control. All of this makes data exchange more difficult.
The issue can be addressed by constructing a data-centric structure that is the foundation for data flow between partners, suppliers, and customers in the data ecosystem. The data is separated from the applications that use this data by organizing it through a specific data hub.
Challenges of Digitalization in Manufacturing
As with any other sector, many factors can stop manufacturers from taking part in digital transformation projects, whether pitching the concept to management or fighting the fear of personnel and business resources.
But, beginning discussions can provide manufacturers with an honest review of their weaknesses and their processes for allocating resources and even open them to the latest technologies.
-
Any digital transformation project could put pressure on your IT department's technological stack and development framework. This may mean implementing new releases or processes, APIs, or developing new domains of the digital infrastructure performance.
-
Digitalization in the manufacturing sector results in the loss of employees: workers are often discontented with new workplace conditions and demands. The reluctance of employees and issues with communication is also major challenge for manufacturers.
-
In a highly dynamic and cash-sensitive business, manufacturers must consider the budgetary and investment restrictions with care. This can cause doubts regarding sticking to the factory's digital transformation strategy.
-
Manufacturing operations can be complicated due to strict schedules and a variety of resources limitations. This is why management does not like adverse effects on operations before experiencing any benefits resulting from their digital transformation in manufacturing.
Although starting a digital transformation process can be a challenge, it's best not an all-inclusive undertaking. There are various digital transformation experts and advisory services to aid manufacturers on their journey. In addition, numerous manufacturing stories of success with digital transformation and case studies illustrate how companies made the most of intelligent manufacturing.
Want More Information About Our Services? Talk to Our Consultants!
The Key Takeaway
The best way to start an industrial digital transformation is to find improvements that can yield significant benefits for the consumer.
Are you ready to take that next step toward the digital transformation you've always wanted? If you're looking to create a fantastic bright manufacturing unit that will help enhance your business processes and help you grow, then contact us.