Maximizing ROI: The Cost and Benefits of Adopting Sharepoint And Microsoft Dynamics For Manufacturing for Your Business
- Sharepoint and Microsoft Dynamics for Manufacturing - Detailed Analysis by Enterprise Solutions Experts
Request A Free Consultation - Why Use Sharepoint And Microsoft Dynamics For Manufacturing
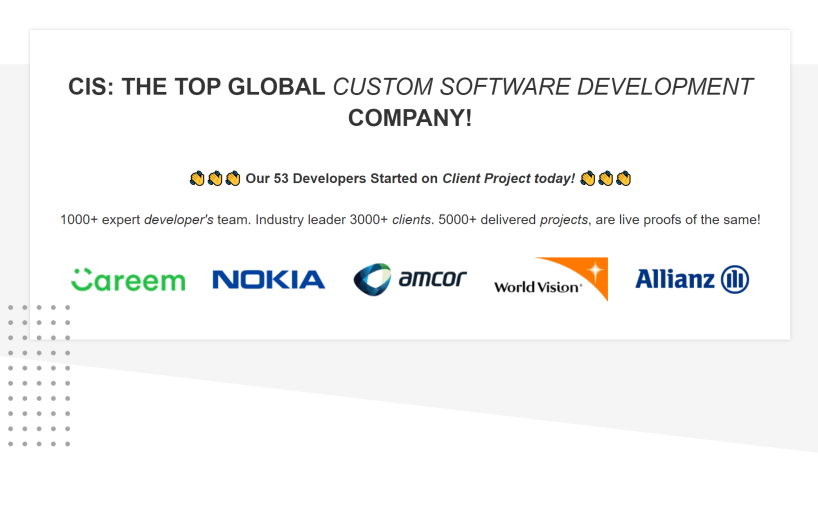
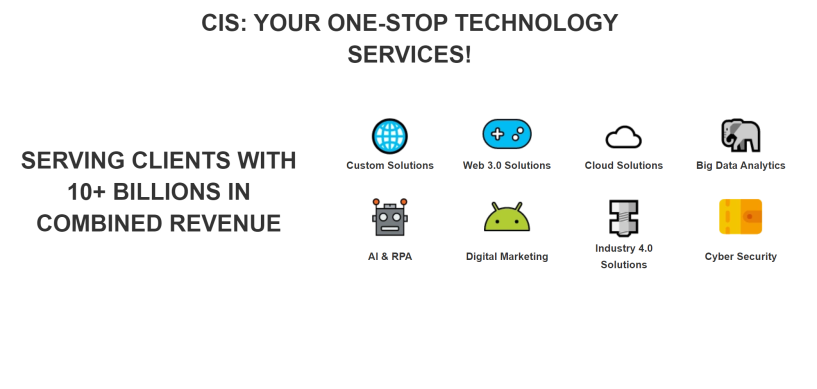
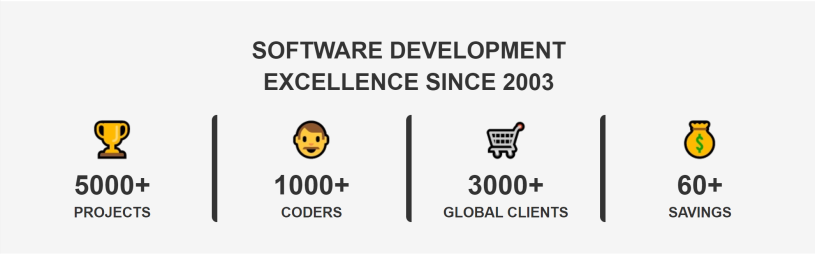
Why Mid-size Companies and Enterprises needs Sharepoint And Microsoft Dynamics For Manufacturing:
Sharepoint and Microsoft Dynamics for Manufacturing are two powerful tools that provide mid-size companies and enterprises with the ability to manage their operations more efficiently. Sharepoint allows users to easily collaborate on projects, documents, and tasks while Microsoft Dynamics provides a comprehensive suite of solutions for managing financials, customer relations, sales orders, inventory control, production planning, supply chain management and much more. Together they offer an integrated platform that can help streamline operations across departments in organizations of all sizes. With this combination of tools businesses have access to real-time data insights which can be used to make better decisions faster. Additionally they enable teams to work together remotely from any device - providing greater flexibility when it comes to meeting deadlines or responding quickly to customer needs.
Benefits of using Sharepoint And Microsoft Dynamics For Manufacturing in Mid-size companies and Enterprises:
1. Increased Collaboration:
SharePoint and Dynamics help streamline collaboration across departments, teams, and external stakeholders by providing a central platform for document sharing, team communication, task management, and more. This helps to ensure that everyone is on the same page in terms of project timelines and expectations.
2. Improved Efficiency:
By having all data stored in one place with easy access from any device or location, users can quickly find what they need when they need it without wasting time searching through multiple systems or folders. This allows for faster decision-making as well as improved customer service response times.
3. Automated Processes:
With SharePoint and Dynamics, companies can automate mundane tasks such as generating reports or tracking inventory levels so employees have more time to focus on higher value activities that require their expertise instead of spending hours manually entering data into spreadsheets or other software programs.
4. Enhanced Security:
Both solutions come with robust security features including encryption technology which ensures sensitive information remains secure at all times while still allowing authorized personnel access to the necessary data needed to make informed decisions quickly and accurately without compromising security protocols.Detailed Features of Sharepoint And Microsoft Dynamics For Manufacturing for Mid-size companies and Enterprises:
1. Automated Workflows:
SharePoint and Dynamics provide automated workflows to streamline manufacturing processes, such as order processing, inventory management, product lifecycle management (PLM), and supply chain management.
2. Data Management:
Both applications offer powerful data management capabilities that allow users to store and analyze large amounts of information related to their production activities. This includes tracking customer orders, managing inventories, monitoring quality assurance protocols, and more.
3. Business Intelligence & Analytics:
With SharePoint and Dynamics for Manufacturing you can gain insights into your business operations through real-time dashboards and analytics tools that help identify trends in production performance or areas where improvements are required.
4. Collaboration Tools:
These solutions also provide collaboration tools like chat rooms for internal communication, document sharing for easy access to important documents across departments or locations within the organization, project boards for tracking progress on tasks assigned during the manufacturing process etc..
5. Customization & Integration:
You can customize both applications according to your specific needs by adding custom fields or integrating with third-party systems such as ERP software or other business intelligence tools if needed.
6 Security Features :
Both platforms come with robust security features including role-based permission settings so only authorized personnel have access to sensitive data related to production activitiesRequest A Quote - Why Use Sharepoint And Microsoft Dynamics For Manufacturing
Who are the Users of Sharepoint And Microsoft Dynamics For Manufacturing:
The customers using Sharepoint and Microsoft Dynamics for Manufacturing are typically mid-sized to large manufacturing companies, such as automotive manufacturers, food and beverage processing plants, chemical producers, and other industrial organizations.
How to ensure Data Security and Compliance with Sharepoint And Microsoft Dynamics For Manufacturing:
1. Ensure Data Encryption:
All data stored in Sharepoint and Microsoft Dynamics for Manufacturing should be encrypted to ensure that only authorized users have access to the information. This can be done using encryption protocols such as AES or RSA, which are available on both platforms.
2. Implement Access Controls:
It is important to implement access controls so that only those with the necessary permissions can view and modify sensitive data within Sharepoint and Microsoft Dynamics for Manufacturing. This includes setting up user roles, groups, and permission levels accordingly so that unauthorized individuals cannot gain access to confidential information. Additionally, administrators should regularly review user accounts for any suspicious activity or changes in privileges granted over time.
3. Establish a Backup Plan:
Having a reliable backup plan in place is essential for ensuring compliance with regulations regarding data security and privacy of customer information stored within Sharepoint and Microsoft Dynamics for Manufacturing systems. Backups should be taken frequently (e.g., daily) and securely stored off-site in order to protect against potential disasters or malicious attacks that could result in loss of critical business information or other damage caused by hackers or malware infections.
4 . Monitor Activity Logs :
Regularly monitoring activity logs within SharePoint will help identify any suspicious behavior associated with accessing sensitive data stored within the system - this could include attempts at unauthorized logins, file downloads/uploads, etc.. By keeping track of these activities it will be easier to quickly detect any issues before they become serious problems requiring further investigation into possible breaches of security policy/regulations governing usage of personal customer information held by your organization's IT systemsHow Sharepoint And Microsoft Dynamics For Manufacturing can increase organization Productivity, Agility, and Profitability:
Sharepoint and Microsoft Dynamics for Manufacturing can increase organization productivity, agility, and profitability by providing a comprehensive suite of tools to manage the end-to-end manufacturing process. The platform provides an integrated view of all aspects of production from planning through execution. It also allows organizations to track inventory levels in real time, optimize supply chain processes, improve customer service levels, reduce costs associated with manual data entry or errors caused by multiple systems, and quickly respond to changing market conditions. Additionally, it enables predictive analytics that provide insights into how operations are performing so that businesses can identify areas where improvements can be made or new opportunities explored.
Request A Quote - Why Use Sharepoint And Microsoft Dynamics For Manufacturing
How to Measure KPIs and increase Benefits of implementing Sharepoint And Microsoft Dynamics For Manufacturing in Mid-size companies and Enterprises:
1. Establish measurable KPIs:
Depending on the company's goals and objectives, establish key performance indicators (KPIs) to measure the success of implementing Sharepoint and Microsoft Dynamics for Manufacturing. Examples of potential KPIs include cost savings, increased productivity, improved customer satisfaction, or reduced time-to-market.
2. Track usage data:
Track usage data such as page views, user engagement metrics, and other relevant analytics to gauge the effectiveness of Sharepoint and Microsoft Dynamics in achieving desired outcomes. This will help you identify areas where improvements can be made or new features added to enhance value delivered by these solutions.
3. Analyze customer feedback:
Encourage customers to provide feedback on their experience with Sharepoint and Microsoft Dynamics for Manufacturing through surveys or interviews so that any issues can be addressed quickly before they become a major problem.
4. Monitor operational efficiency:
Monitor operational efficiency metrics such as lead times, order fulfillment cycle times, inventory turnover rates etc., to assess how well these solutions are delivering results in terms of streamlining operations within your organization's supply chain network partners too if applicable..
5 . Evaluate ROI:
Finally evaluate the return on investment (ROI) from deploying Sharepoint and Microsoft Dynamics for Manufacturing by comparing actual costs incurred against expected benefits realized over a given period of timeHow Sharepoint And Microsoft Dynamics For Manufacturing can increase Employee Morale in your organization:
Sharepoint and Microsoft Dynamics for Manufacturing can increase organization employee morale by providing employees with better access to information, improved collaboration capabilities, more efficient processes, and increased visibility into organizational performance. Employees will be able to access the latest data about their own progress as well as that of their colleagues quickly and easily. This will help them stay informed on what's happening in the organization and make sure they are working towards common goals. Additionally, streamlined processes enabled by these tools can reduce manual work and errors while freeing up time for employees to focus on higher-value activities such as innovation or problem solving. Finally, enhanced visibility into organizational performance metrics can provide a sense of accomplishment among employees when they see how their individual efforts contribute to overall success.
How Sharepoint And Microsoft Dynamics For Manufacturing is Better than its Competitors:
Sharepoint and Microsoft Dynamics for Manufacturing offer many advantages over its competitors. These include:
1. Increased efficiency - SharePoint and Dynamics provide users with an integrated system that helps streamline processes, reduce manual data entry, and automate workflows. This can help save time and money by eliminating redundant tasks.
2. Improved collaboration - With SharePoint's built-in document management features, teams can easily collaborate on projects in real-time from anywhere in the world without having to worry about version control or access rights issues. Plus, it integrates seamlessly with other Microsoft products like Office 365 so you can quickly share documents across platforms without any hassle.
3. Comprehensive analytics - With advanced reporting capabilities of both SharePoint and Dynamics, manufacturers are able to gain greater insights into their operations which allows them to make better decisions faster based on accurate information available at a glance.
4 Scalability - Both solutions are capable of scaling up as your business grows allowing you to add new features or modules when needed while still maintaining the same level of performance throughout all stages of growth
Request A Quote - Why Use Sharepoint And Microsoft Dynamics For Manufacturing
Cost to Develop & Implemention of Sharepoint And Microsoft Dynamics For Manufacturing:
The cost of developing and deploying Sharepoint and Microsoft Dynamics for Manufacturing can vary greatly depending on the specific needs of your organization. Generally, you should expect to pay anywhere from $20,000 to $100,000 for a full implementation with customization. This cost includes licenses, installation fees, training costs, consulting fees and ongoing maintenance costs.
Why outsourcing implementation services for Sharepoint And Microsoft Dynamics For Manufacturing is better for Mid-size companies and Enterprises:
Outsourcing implementation services for Sharepoint and Microsoft Dynamics for Manufacturing is better for mid-size companies and enterprises because it allows them to take advantage of the expertise and experience that a specialized service provider can offer. A specialized service provider will be able to provide an end-to-end solution, from initial planning through implementation, training, maintenance, and support. This type of comprehensive approach can help reduce costs while ensuring that the system is implemented correctly. Outsourcing also eliminates the need to hire additional staff or purchase additional hardware or software in order to implement these systems. Furthermore, outsourcing provides access to experts who are familiar with both Sharepoint and Microsoft Dynamics products as well as their integration into manufacturing processes.
Request A Quote - Why Use Sharepoint And Microsoft Dynamics For Manufacturing